Managed to finish most of the exhaust yesterday, well as much as I could without the actual muffler.
I tried to measure the OEM placing of the o2 bung, and drill accordingly to that.
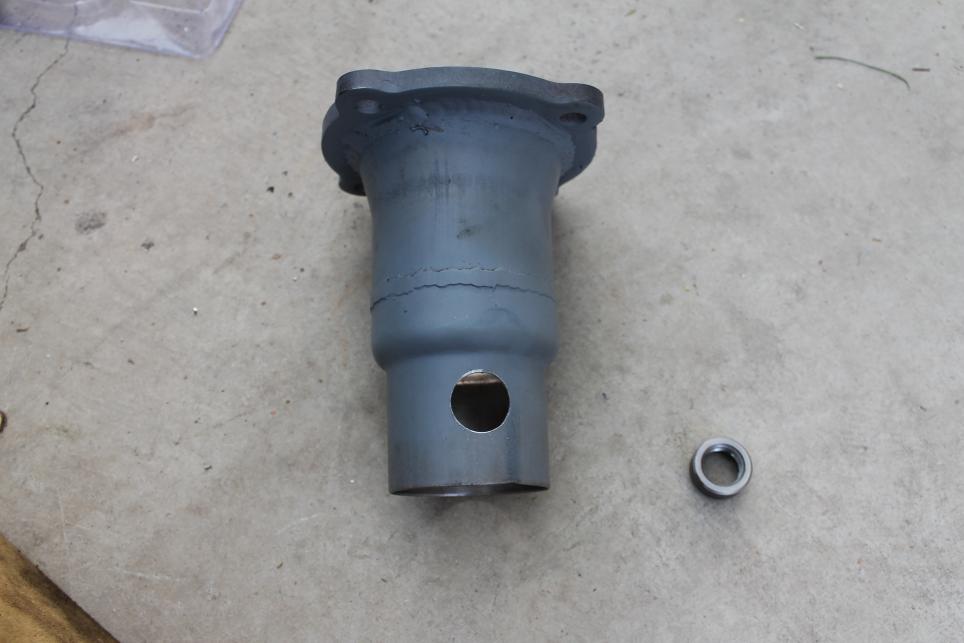
Once that was welded up, I started measuring up where to start the piping. It all consisted of 45deg and 90deg piping.
Here I used the 90deg and welded on the flex pipe.
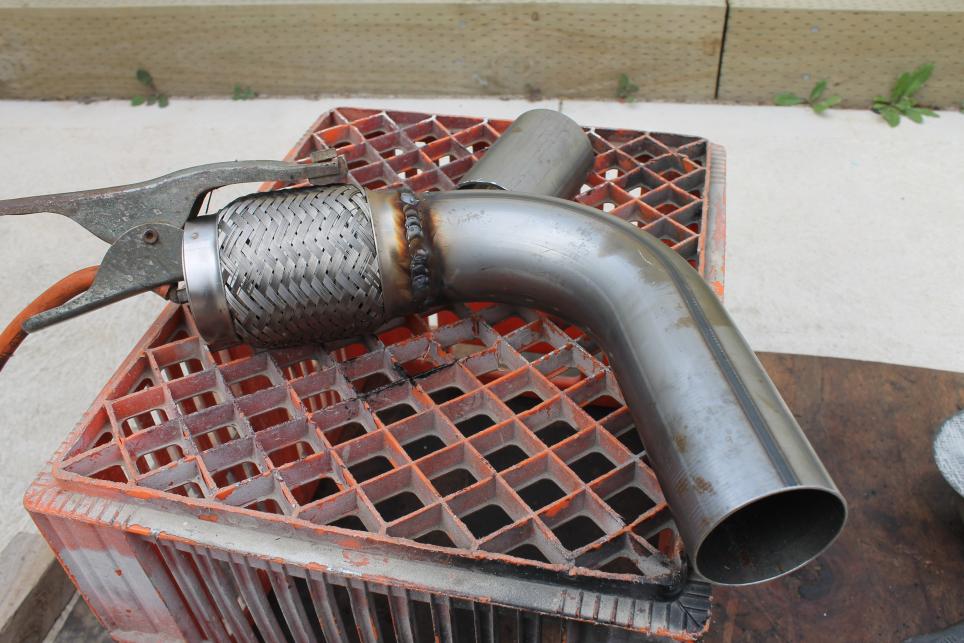
Then a 45deg added to that.
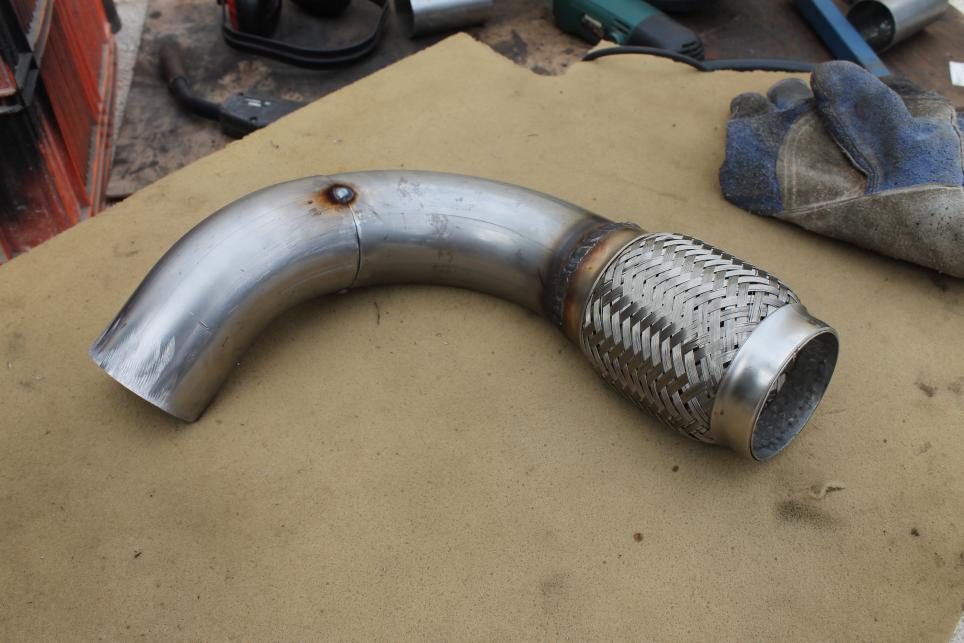
Now all together taking shape.
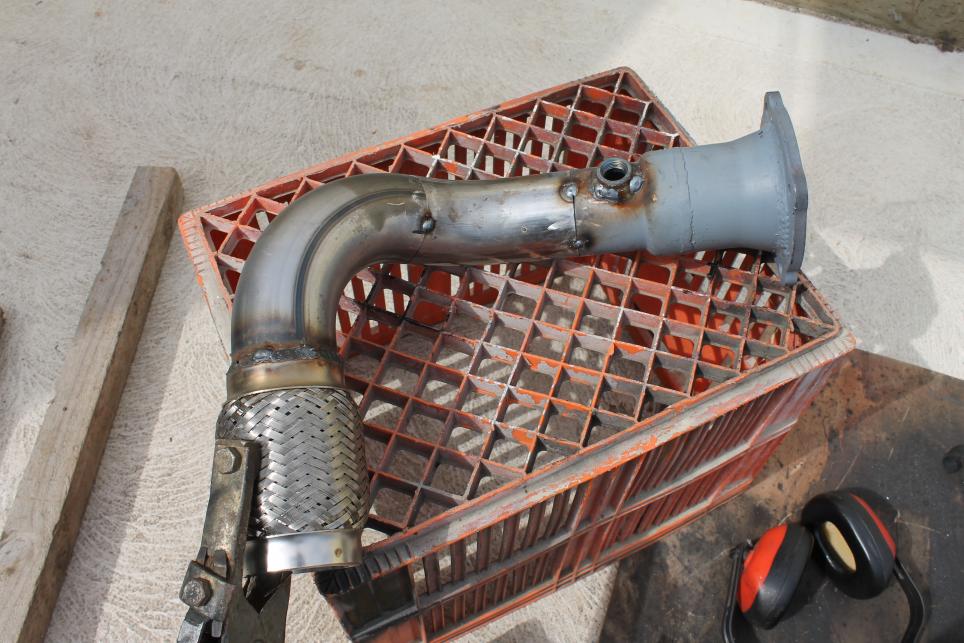
Added another 90deg pipe. This is the shape it will be. A rather straight forward and simple design bending around the engine brace.
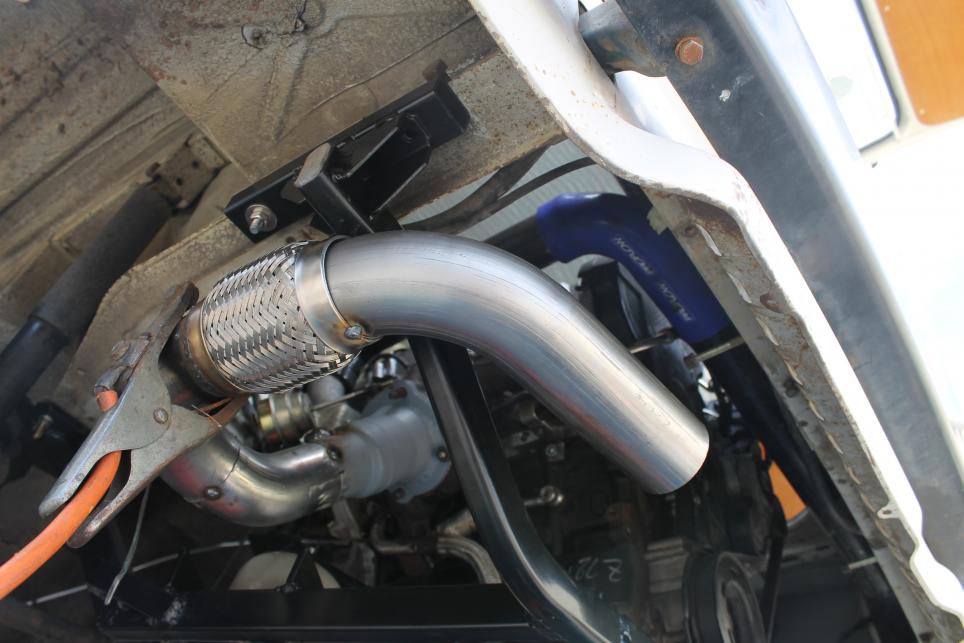
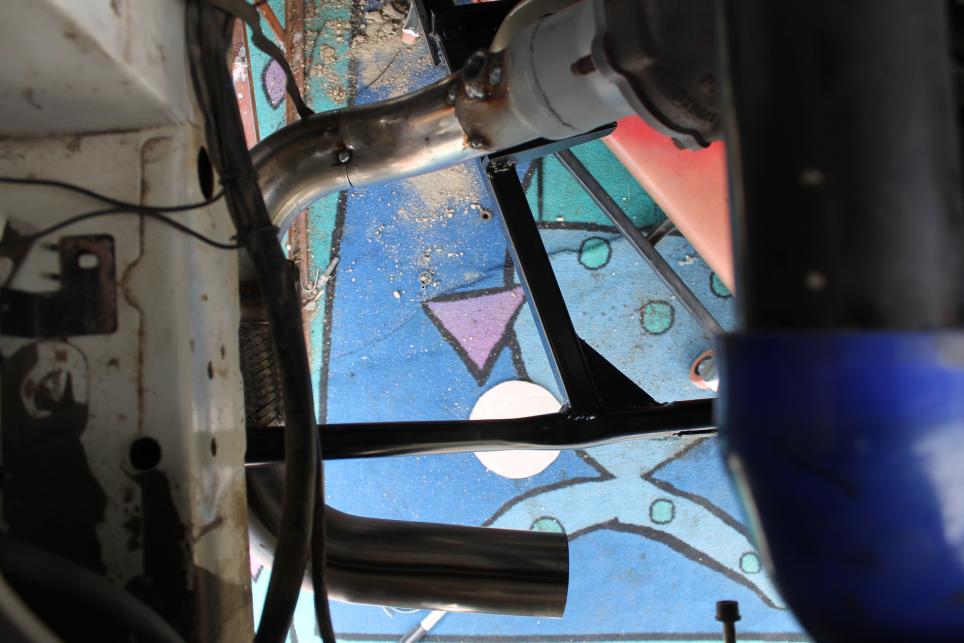
Then I measured and added another straight pipe. The muffler will be welded to the end of this pipe and a nice 3" tip out the side. You can see how the muffler will be sitting in with the template placed at the end.
All welded up nicely and starting to look like an actual exhaust.
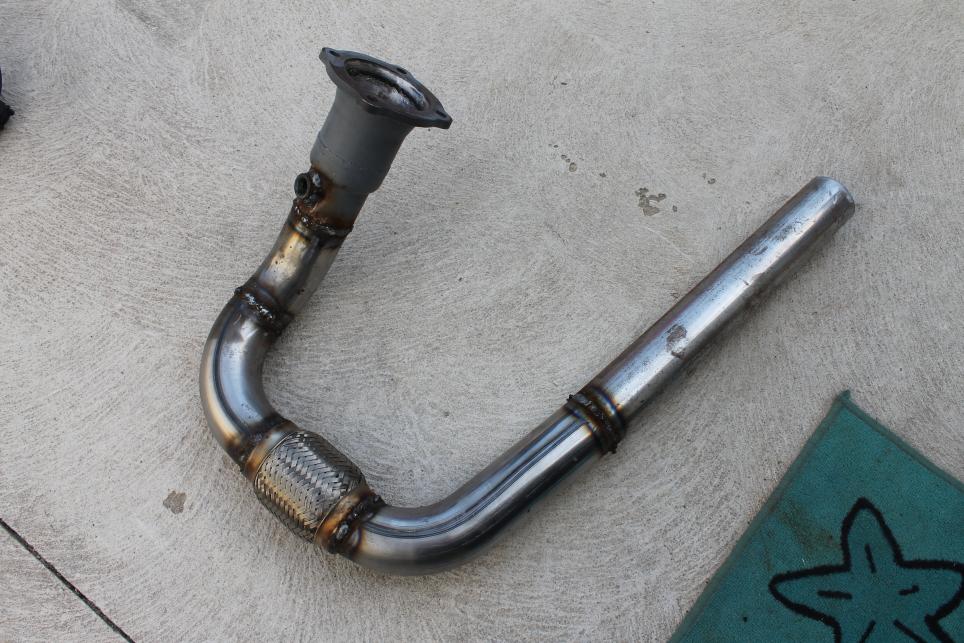
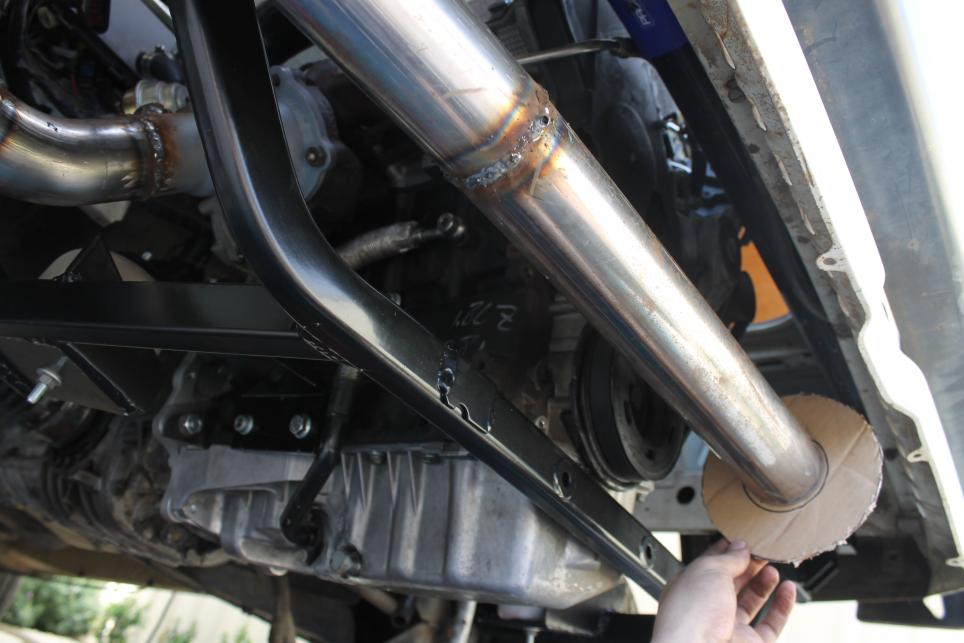
For exhaust hangers, I didn't want to have to weld to the body and make more work to clean/paint it. So after a bit of looking around I found some original bolt holes and came up with a solution.
Found the correct thread and pitched sized bolts, and added a blob of weld to stop the hanger coming off. I went to my buddies workshop and raided his shed for some spare rubber hangers!
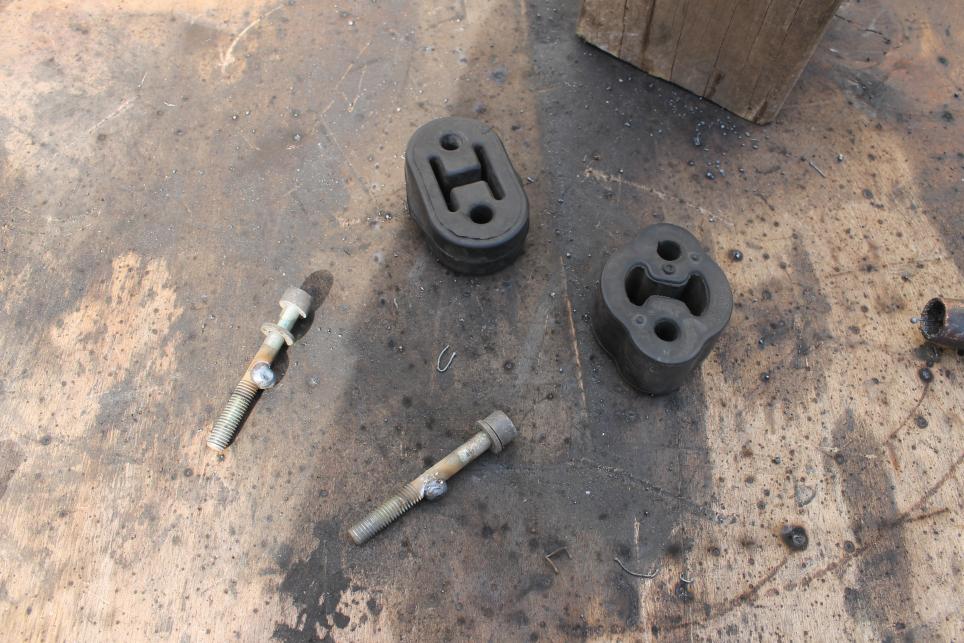
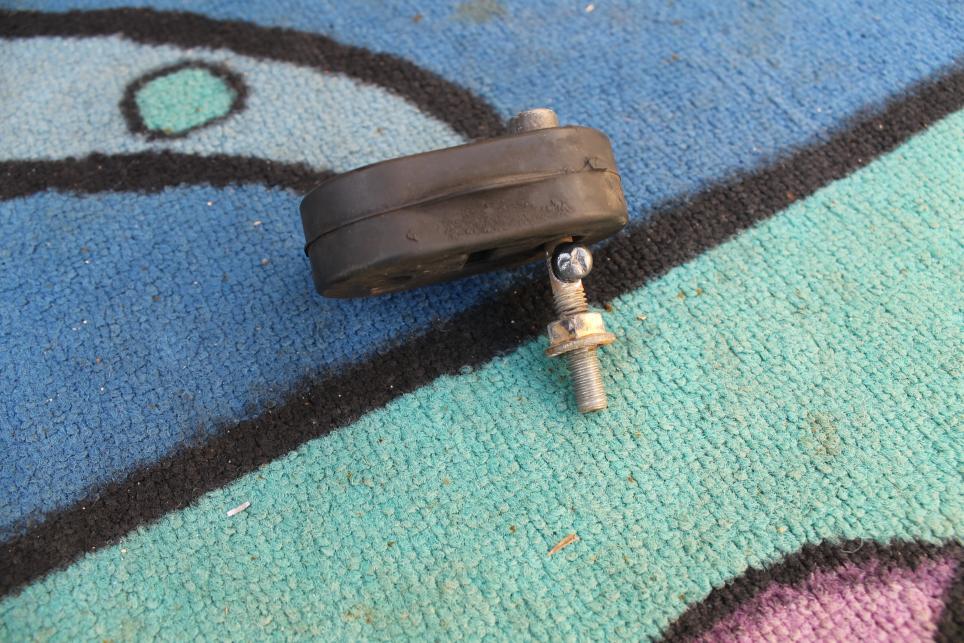
Tested and it fits great!! Happy to have it work out with minimal modification needed.
I was contemplating how much hangers to make, but the piping is really light, so 1 is all I need at this end, and will most likely make another 2, to support the mufflers weight.
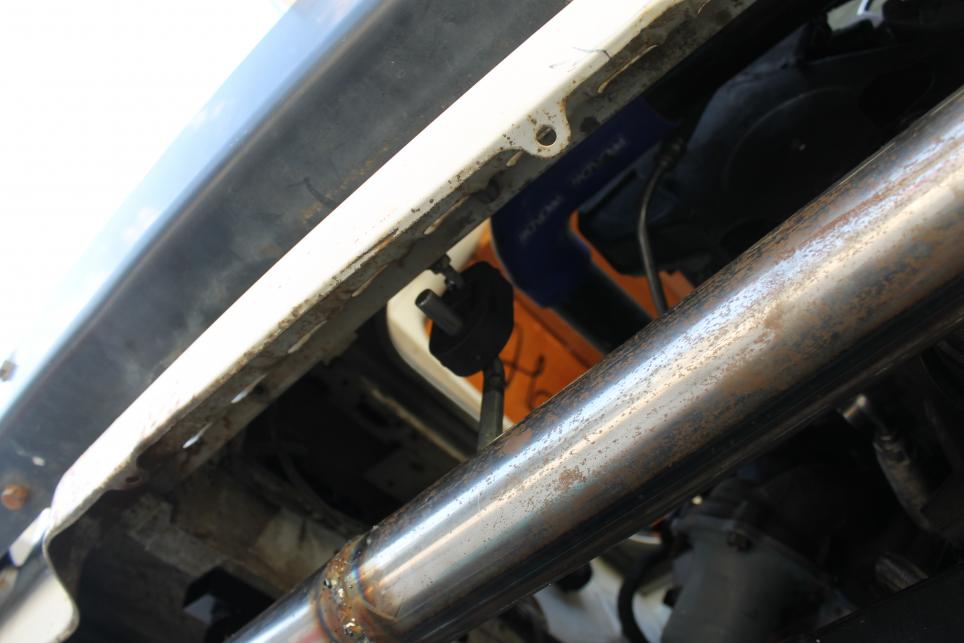
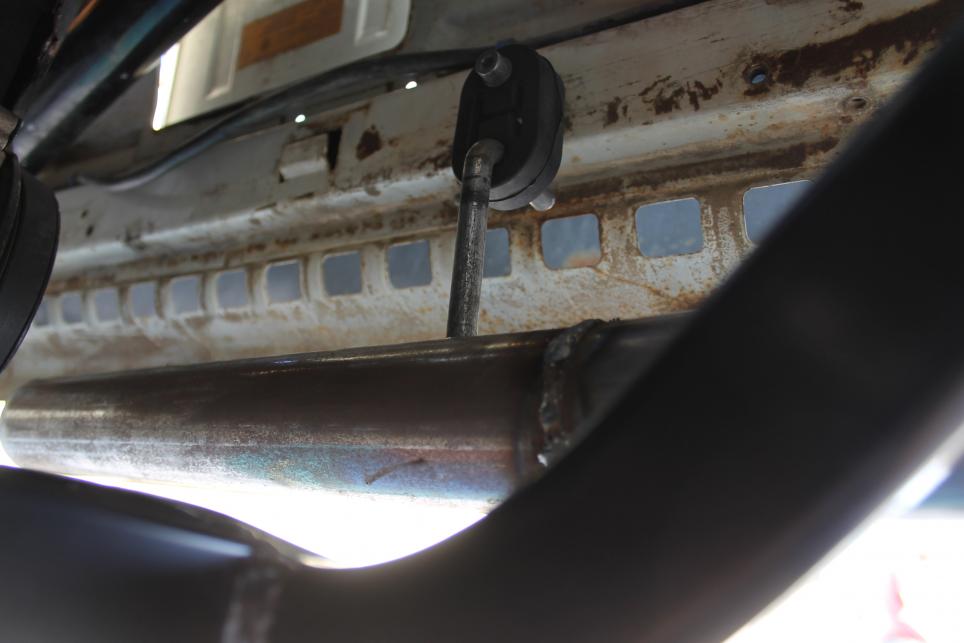
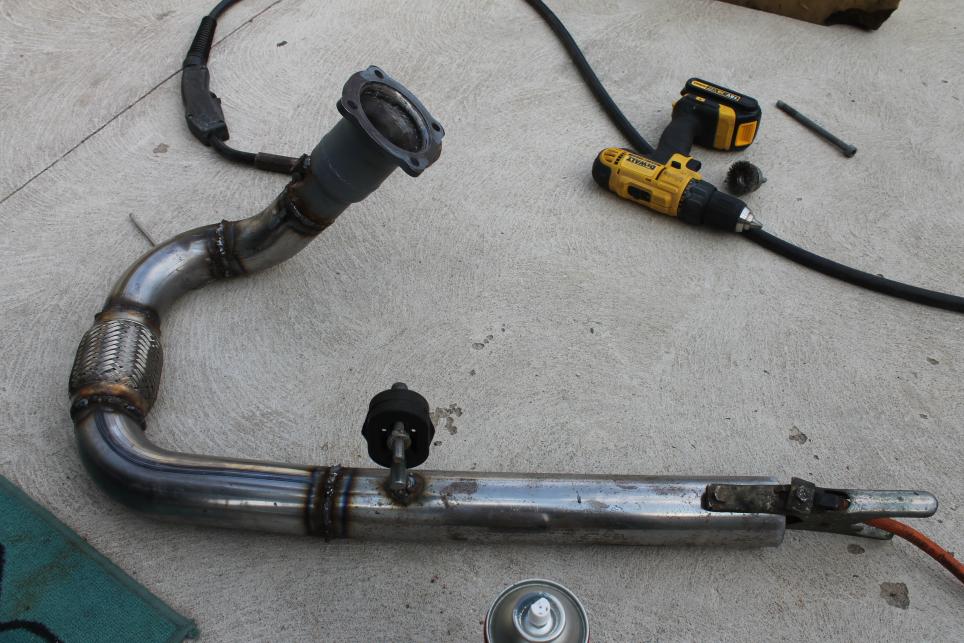
Wire brushed the welds and gave the piping a quick spray in etch. Decided I will wrap up the exhaust to prevent any more heat in the engine bay seeing as its so close.
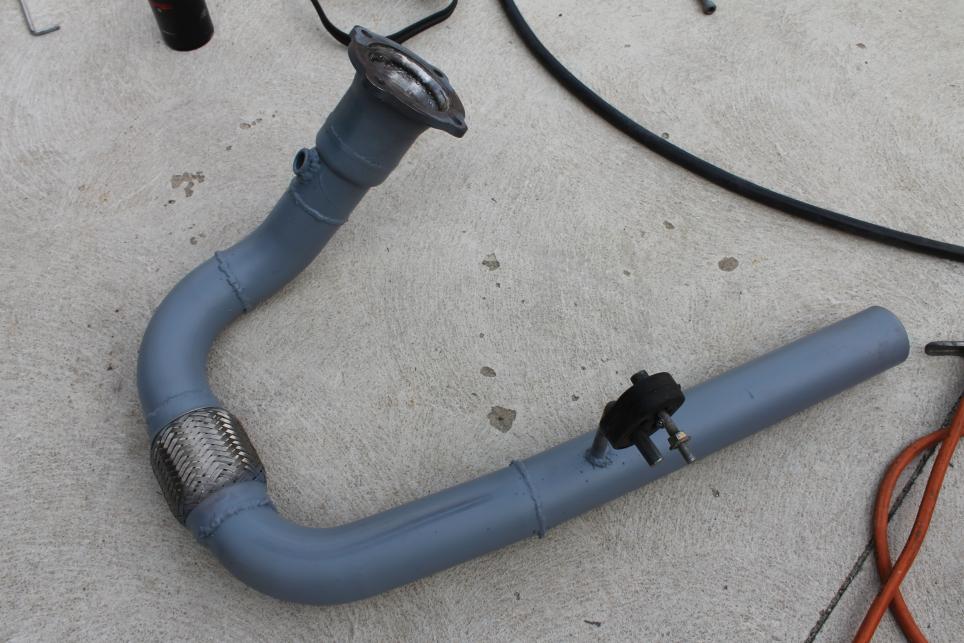
I had a small roll laying around and thought I'd get started on wrapping it. Only lasted half the dump pipe, but I'll get more and finish it all off in time.
Two tips for anyone planning to do this, 1) always wear gloves, as the fibres ITCH!!!! and 2), soak the heat wrap in water before starting.
This allows it to stretch nicely, and when it dries up, its on very snug. Plus it's easier to use when its wet.
I wrapped up a down pipe in the past and didn't get it wet or wear gloves - that led to lots of regret and swearing haha.
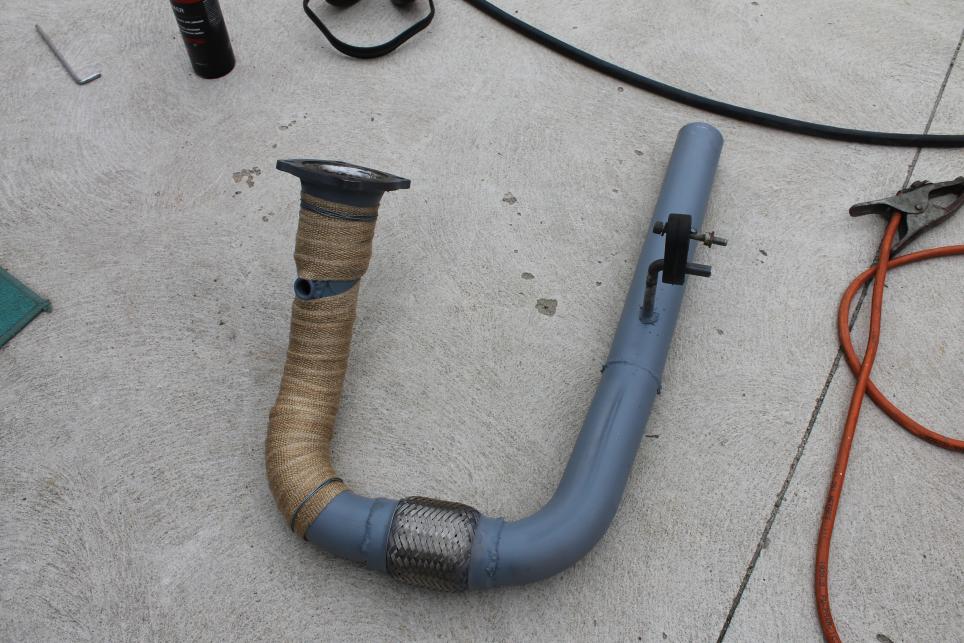
That's all I had time to do yesterday , thanks
I tried to measure the OEM placing of the o2 bung, and drill accordingly to that.
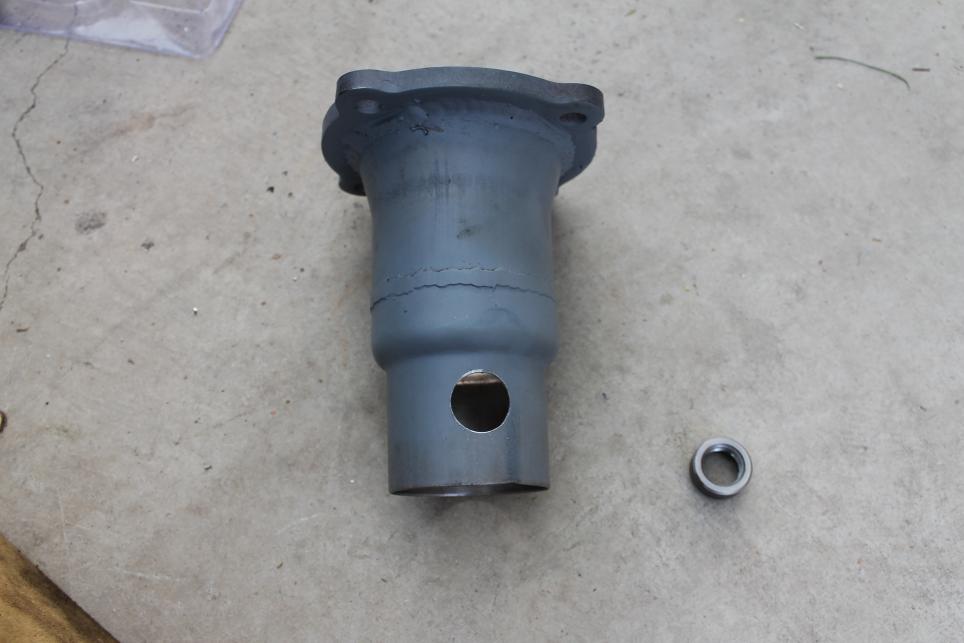
Once that was welded up, I started measuring up where to start the piping. It all consisted of 45deg and 90deg piping.
Here I used the 90deg and welded on the flex pipe.
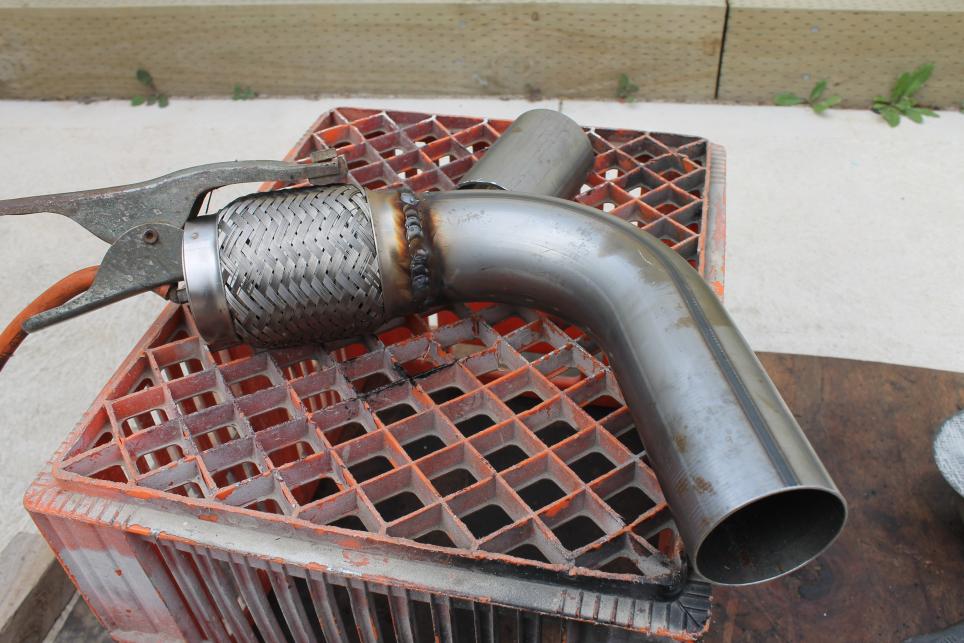
Then a 45deg added to that.
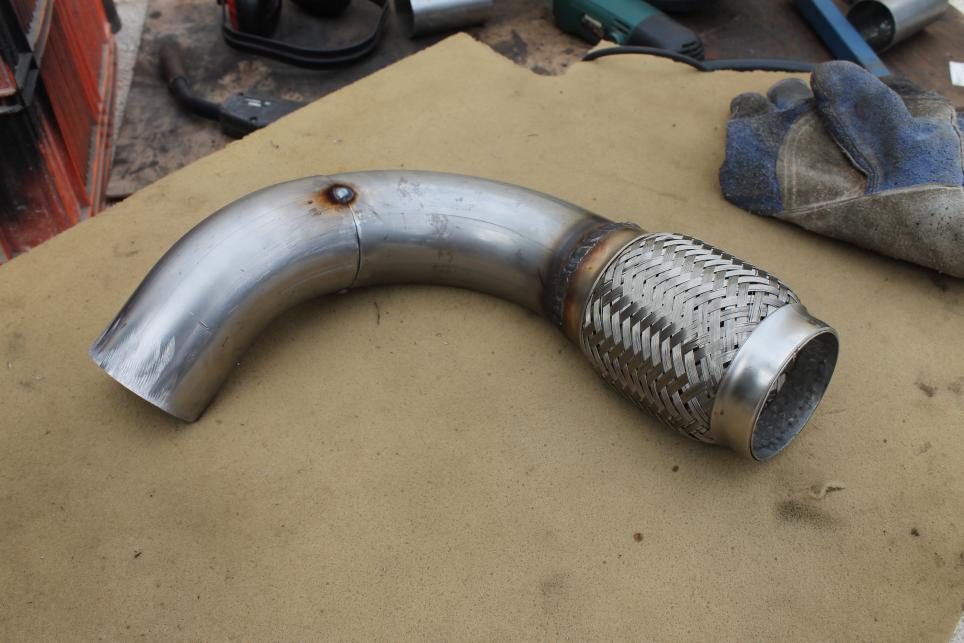
Now all together taking shape.
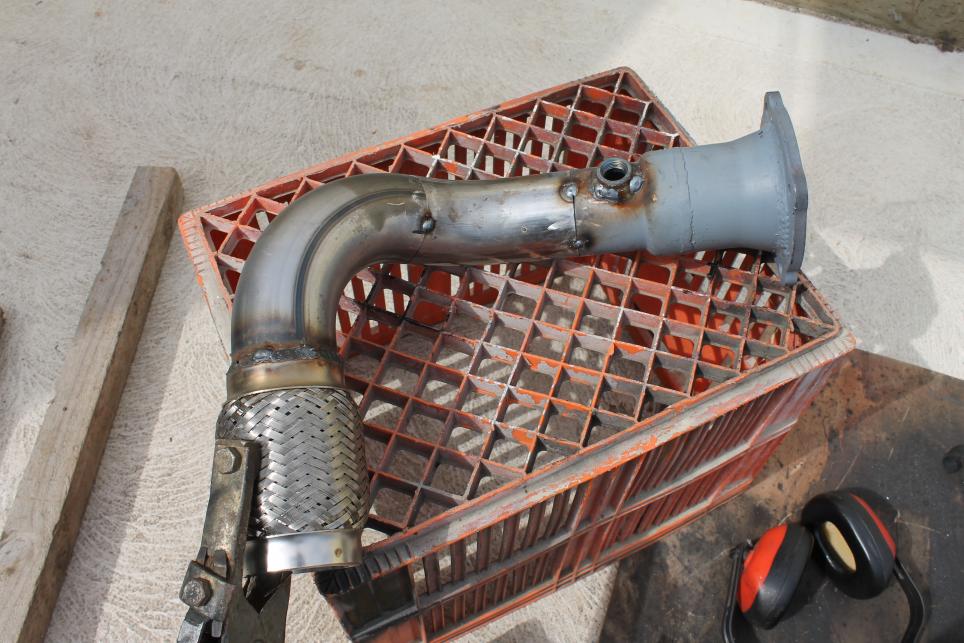
Added another 90deg pipe. This is the shape it will be. A rather straight forward and simple design bending around the engine brace.
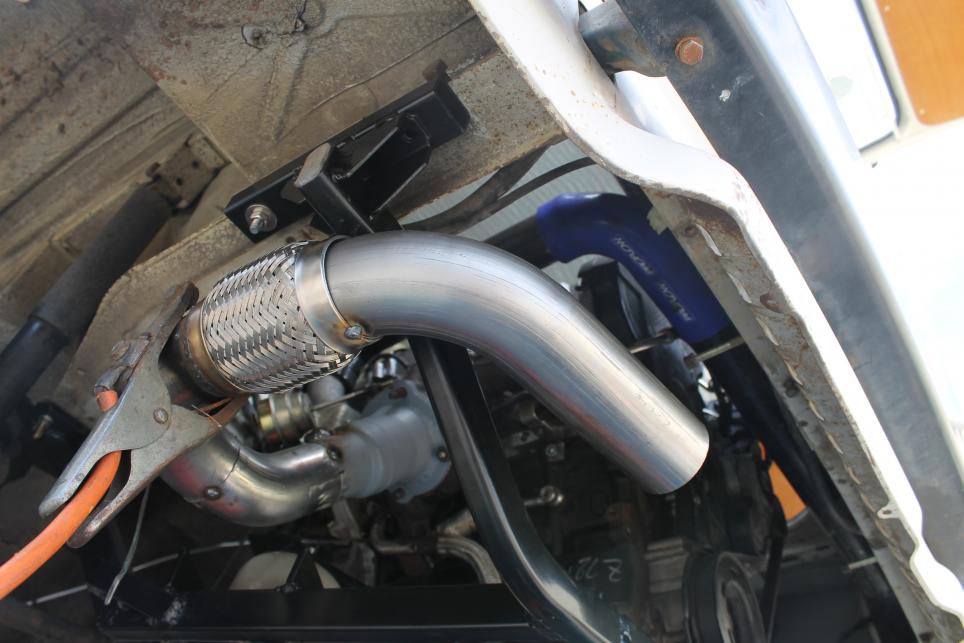
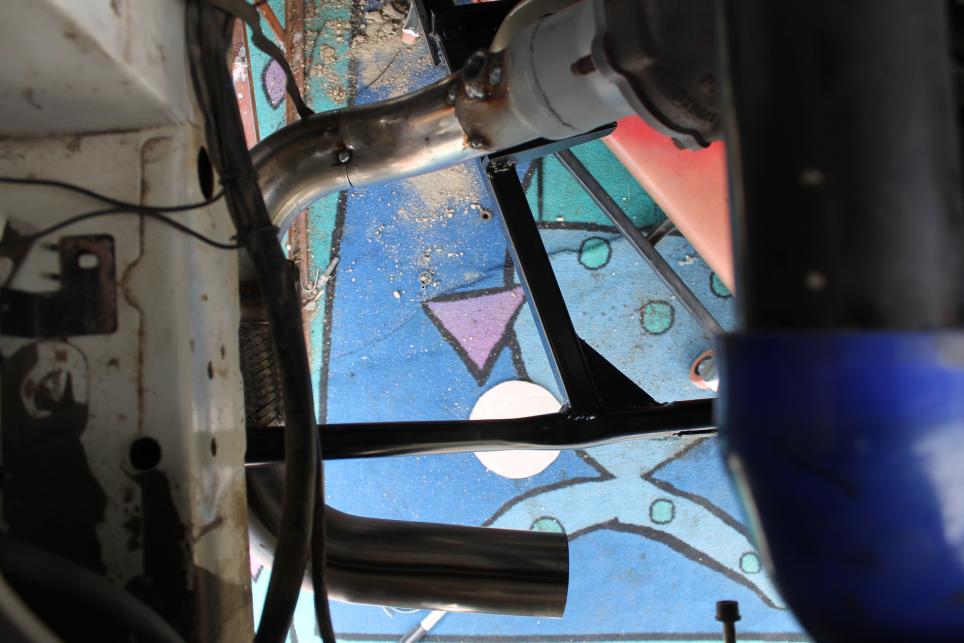
Then I measured and added another straight pipe. The muffler will be welded to the end of this pipe and a nice 3" tip out the side. You can see how the muffler will be sitting in with the template placed at the end.
All welded up nicely and starting to look like an actual exhaust.
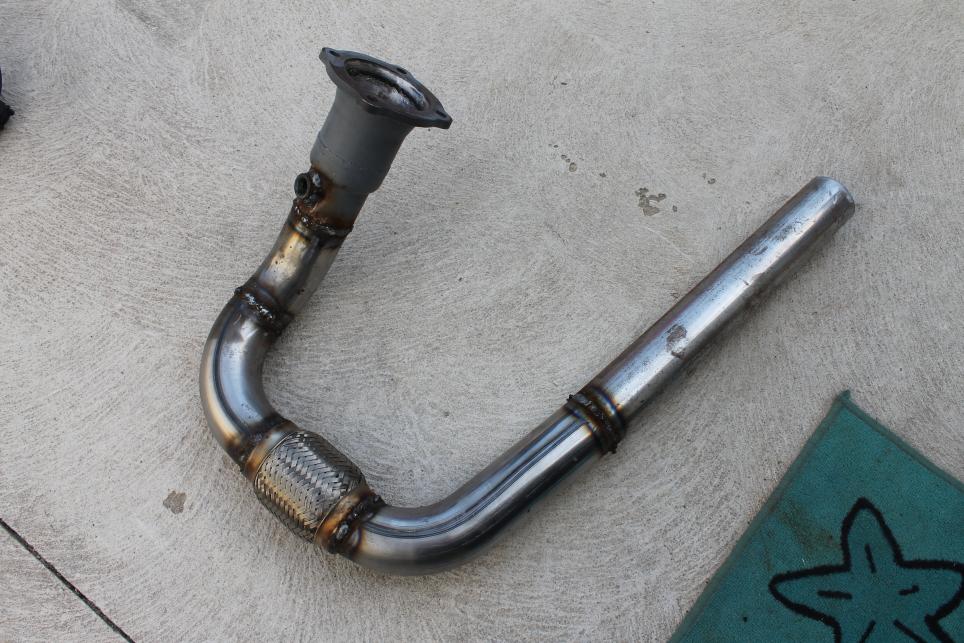
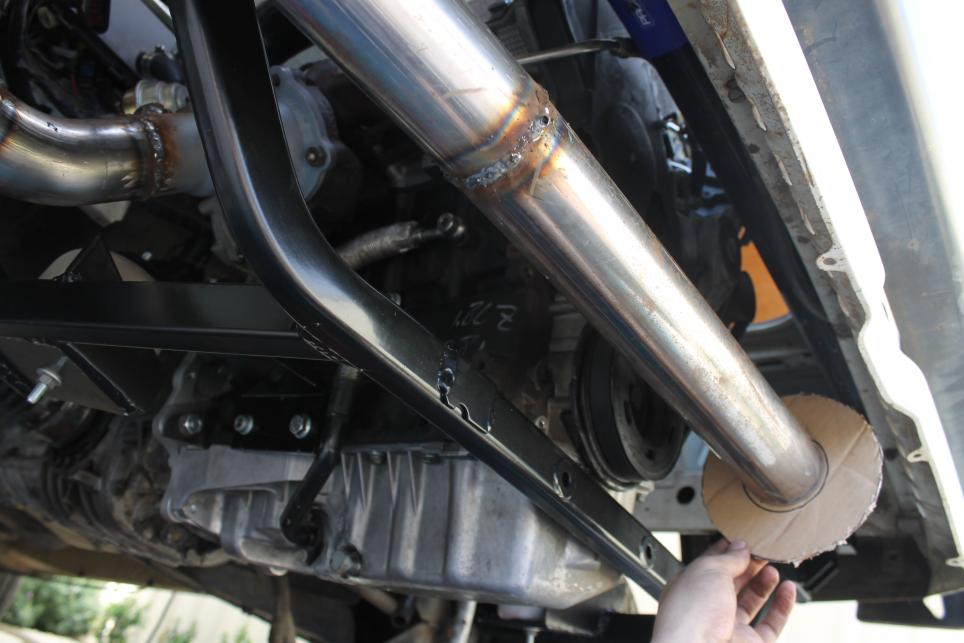
For exhaust hangers, I didn't want to have to weld to the body and make more work to clean/paint it. So after a bit of looking around I found some original bolt holes and came up with a solution.
Found the correct thread and pitched sized bolts, and added a blob of weld to stop the hanger coming off. I went to my buddies workshop and raided his shed for some spare rubber hangers!
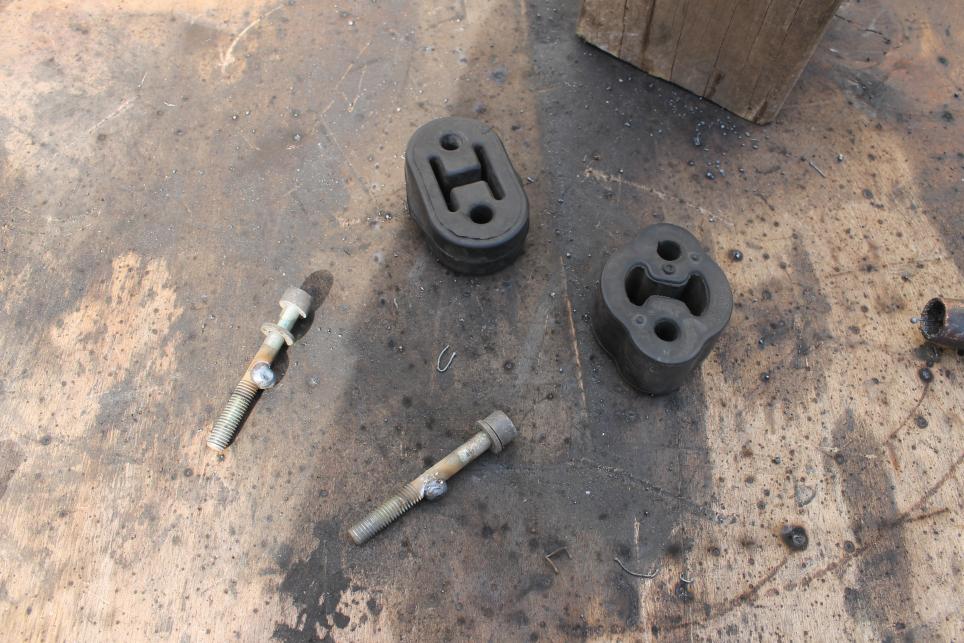
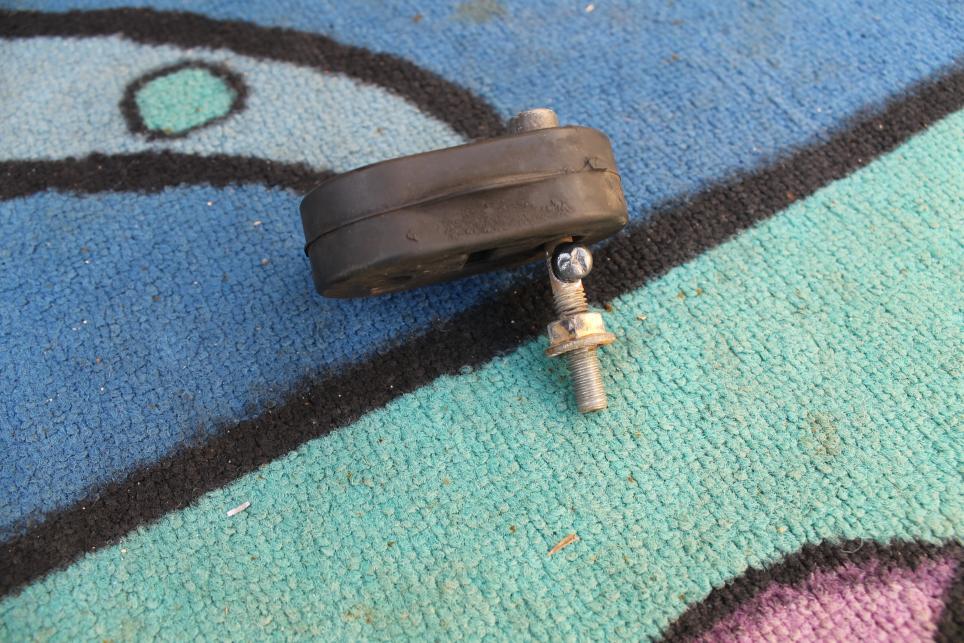
Tested and it fits great!! Happy to have it work out with minimal modification needed.
I was contemplating how much hangers to make, but the piping is really light, so 1 is all I need at this end, and will most likely make another 2, to support the mufflers weight.
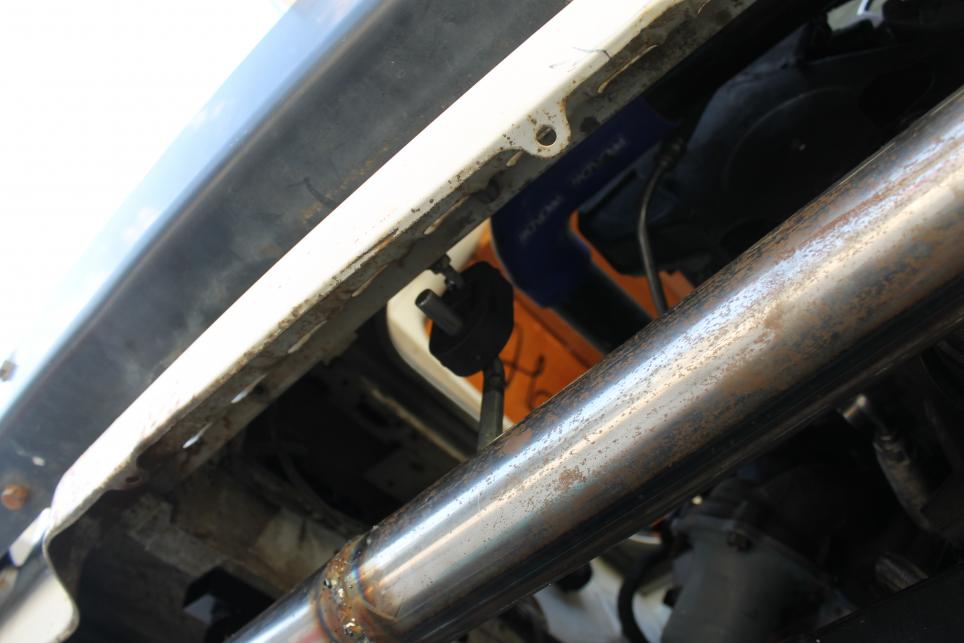
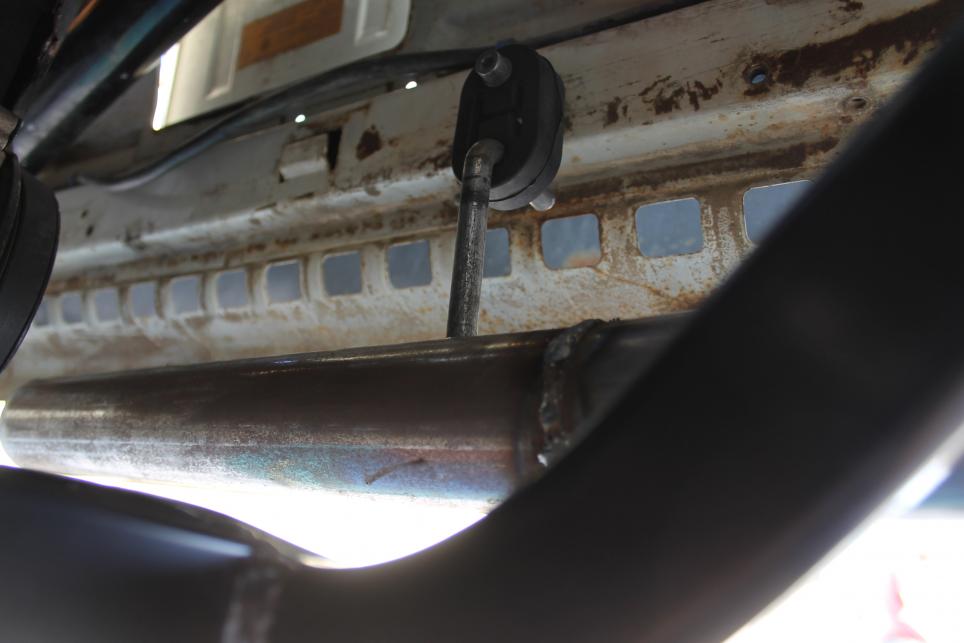
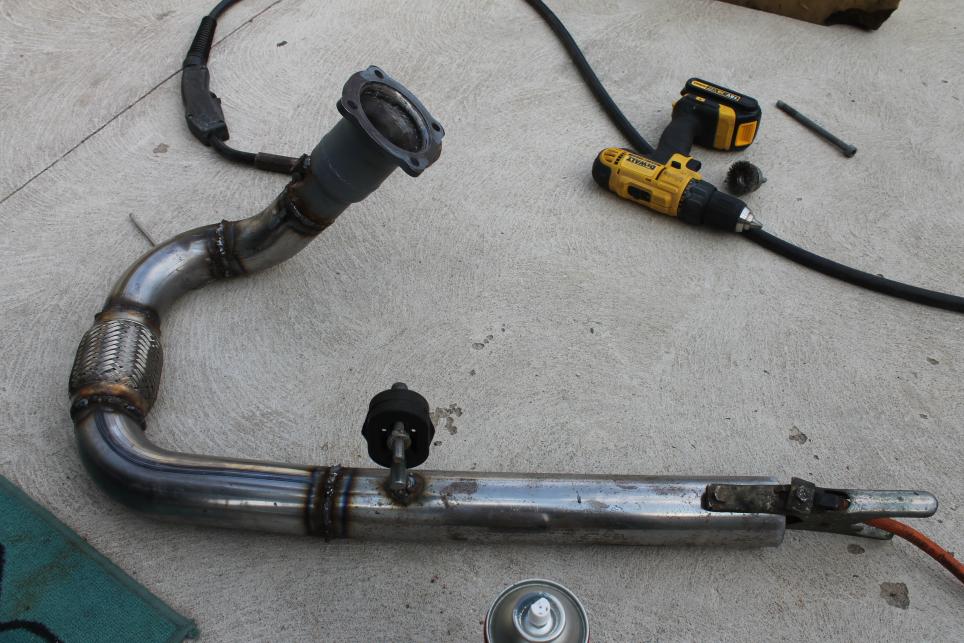
Wire brushed the welds and gave the piping a quick spray in etch. Decided I will wrap up the exhaust to prevent any more heat in the engine bay seeing as its so close.
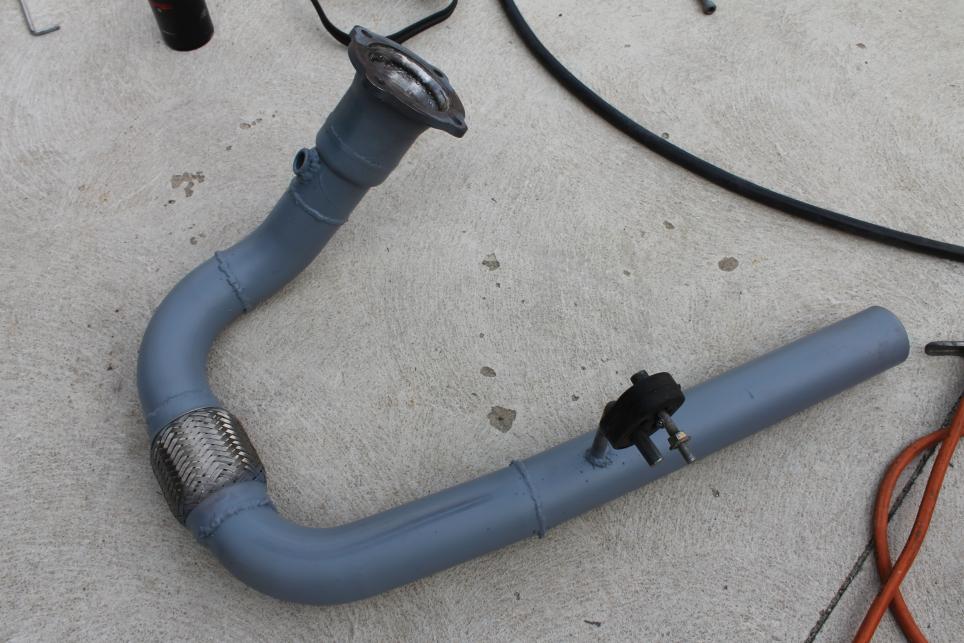
I had a small roll laying around and thought I'd get started on wrapping it. Only lasted half the dump pipe, but I'll get more and finish it all off in time.
Two tips for anyone planning to do this, 1) always wear gloves, as the fibres ITCH!!!! and 2), soak the heat wrap in water before starting.
This allows it to stretch nicely, and when it dries up, its on very snug. Plus it's easier to use when its wet.
I wrapped up a down pipe in the past and didn't get it wet or wear gloves - that led to lots of regret and swearing haha.
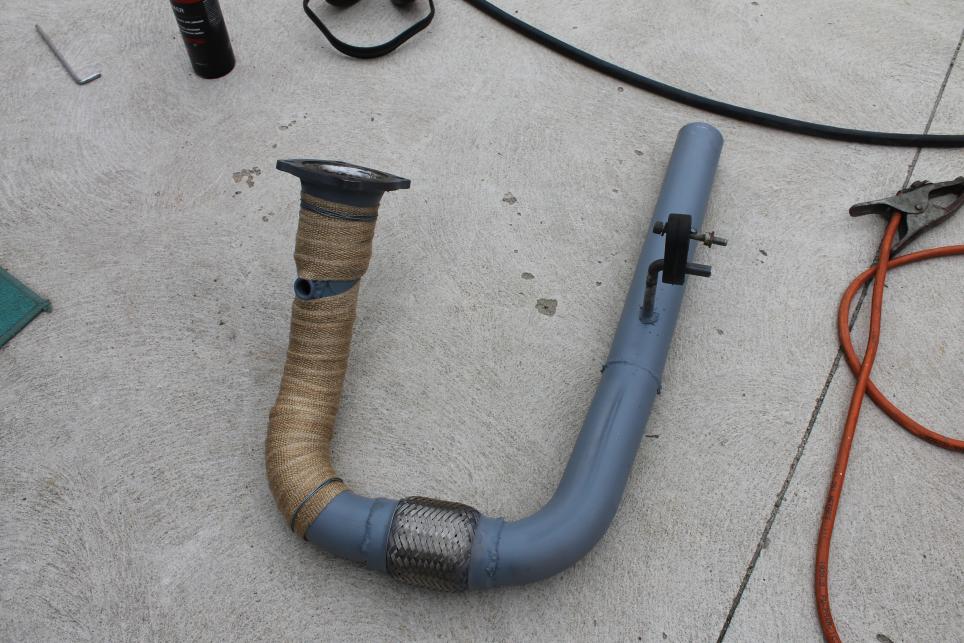
That's all I had time to do yesterday , thanks

Comment