Done for the future reference of all engine gurus worldwide.
Should answer all questions in respect to how far out the 2.0l block can be taken to.
Here we go now, enjoy!
Engine code 6A.
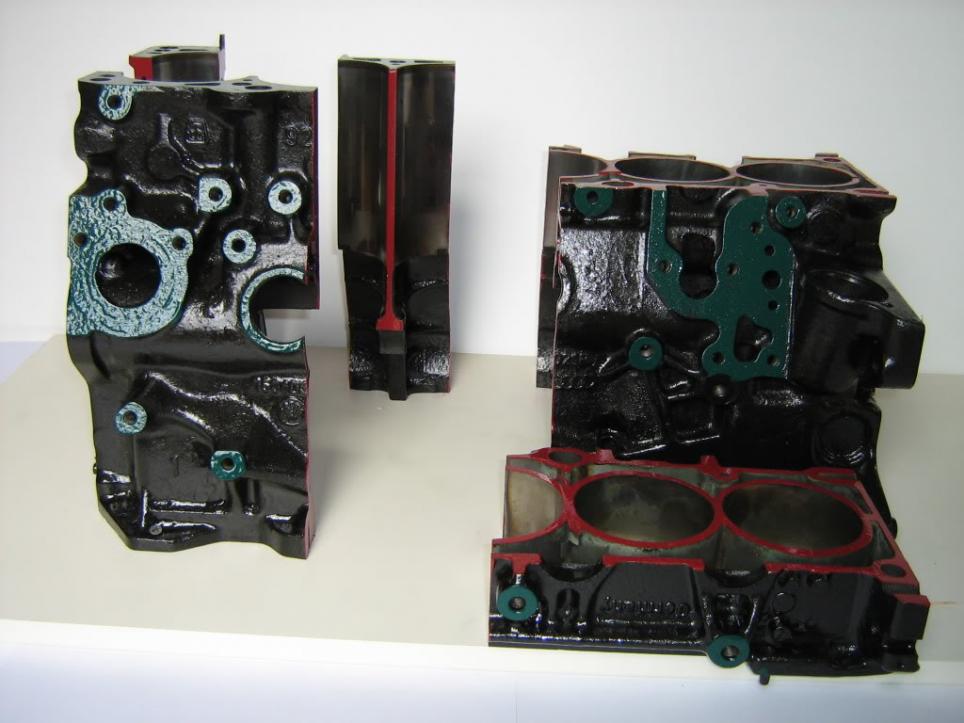
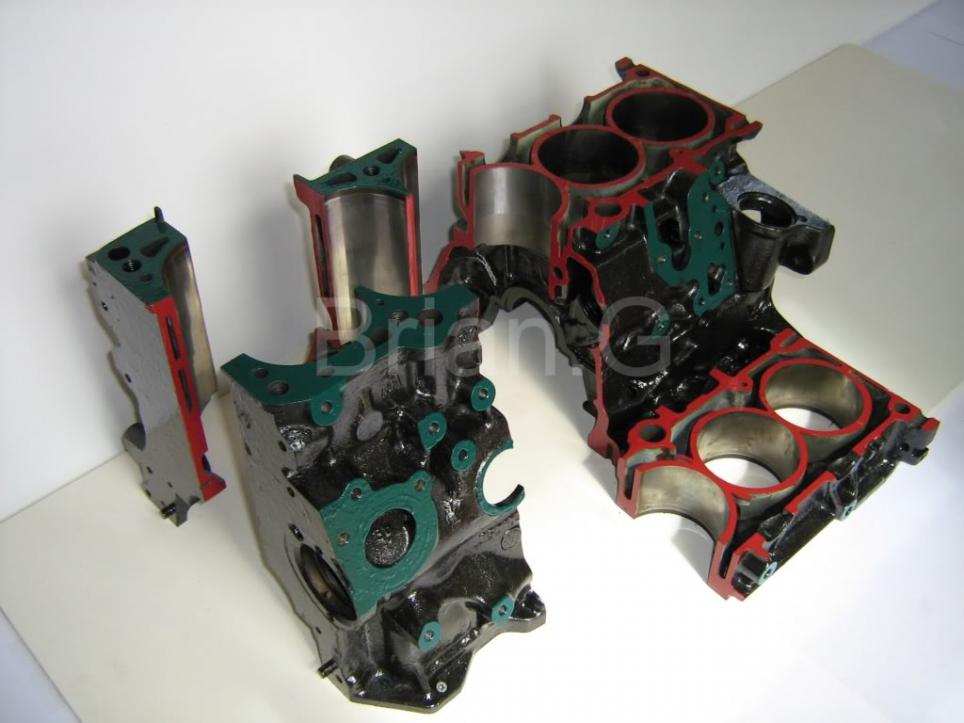
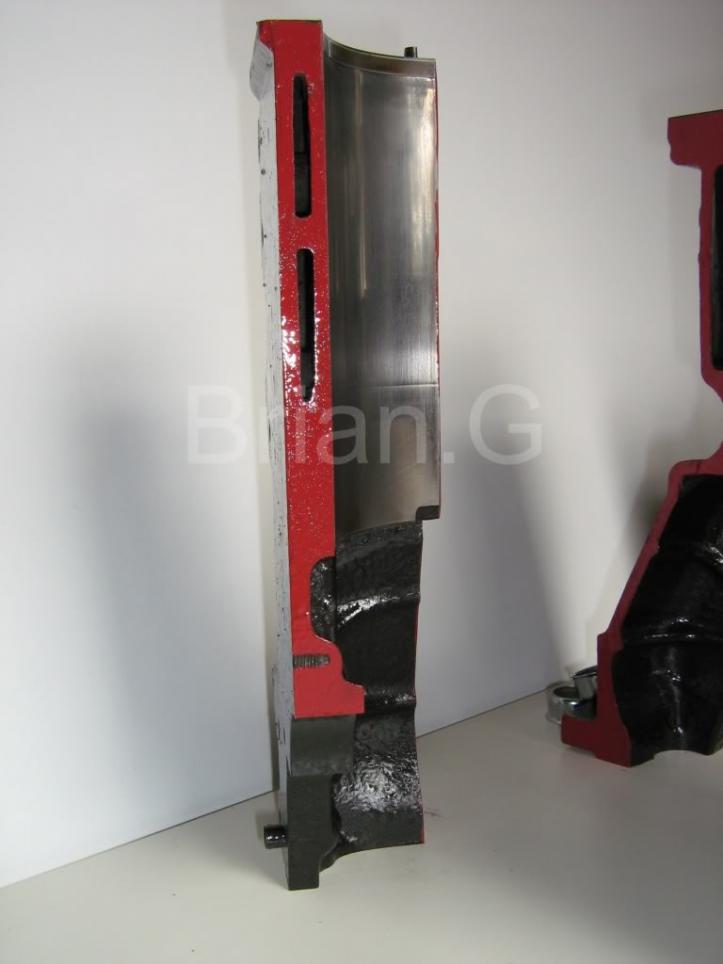
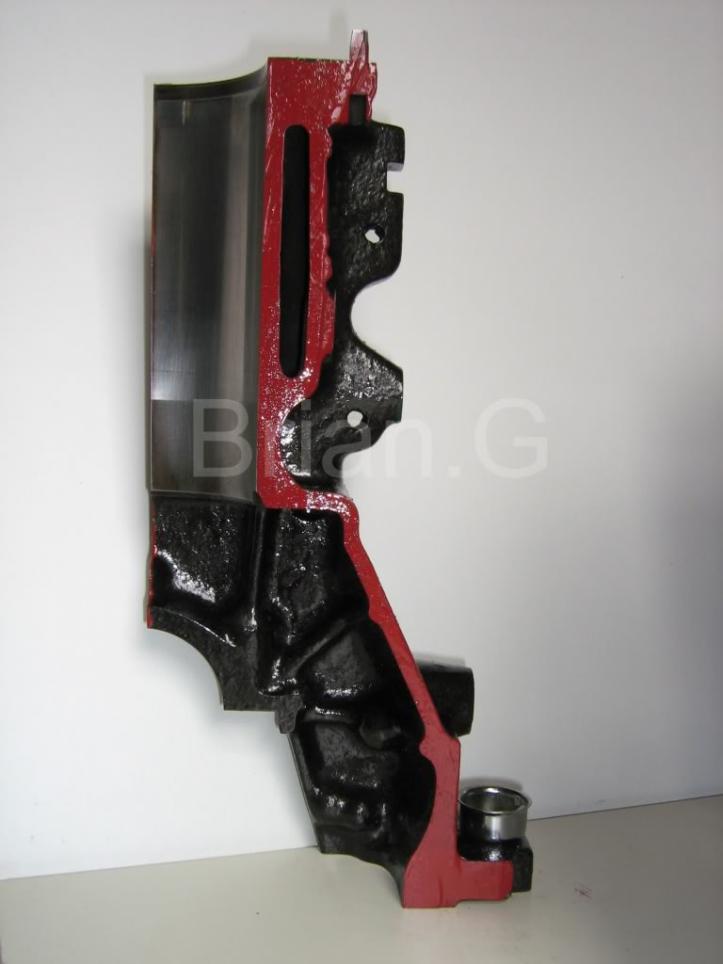
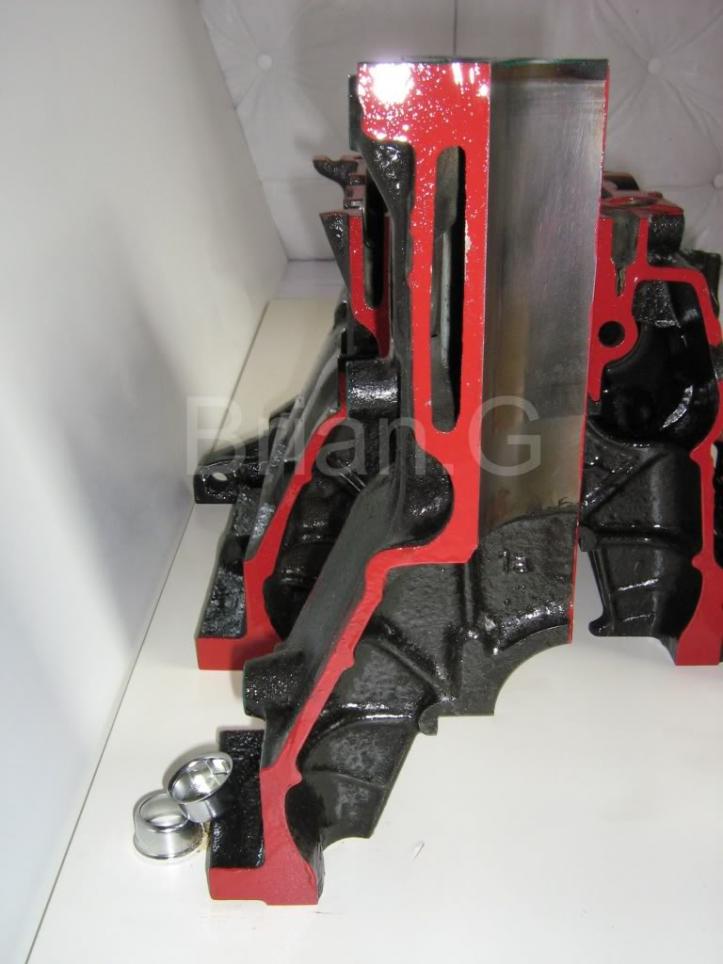
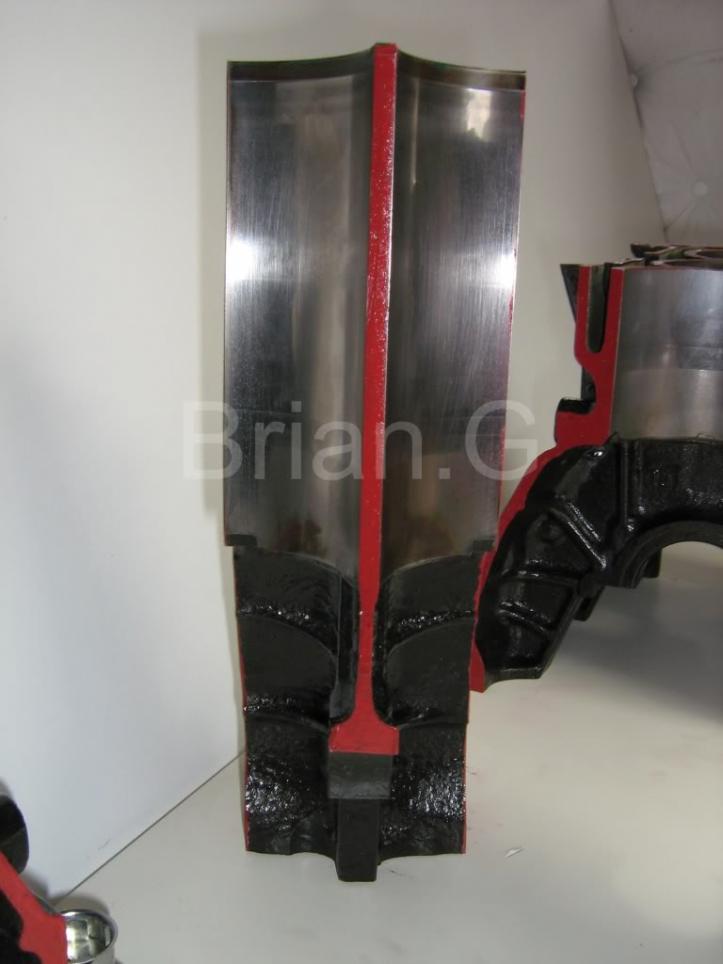
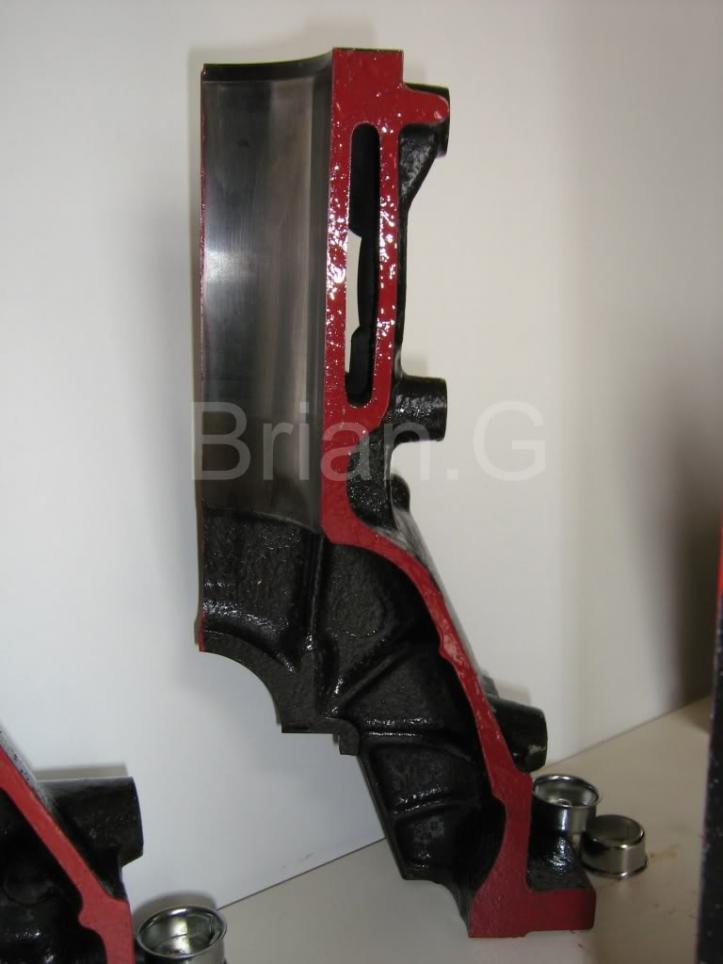
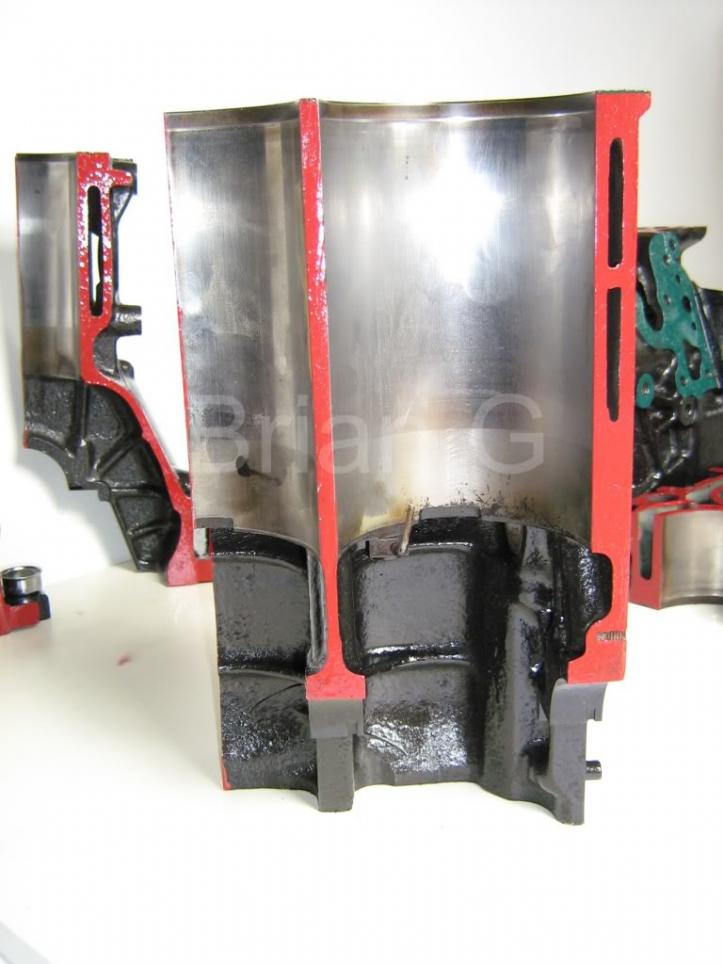
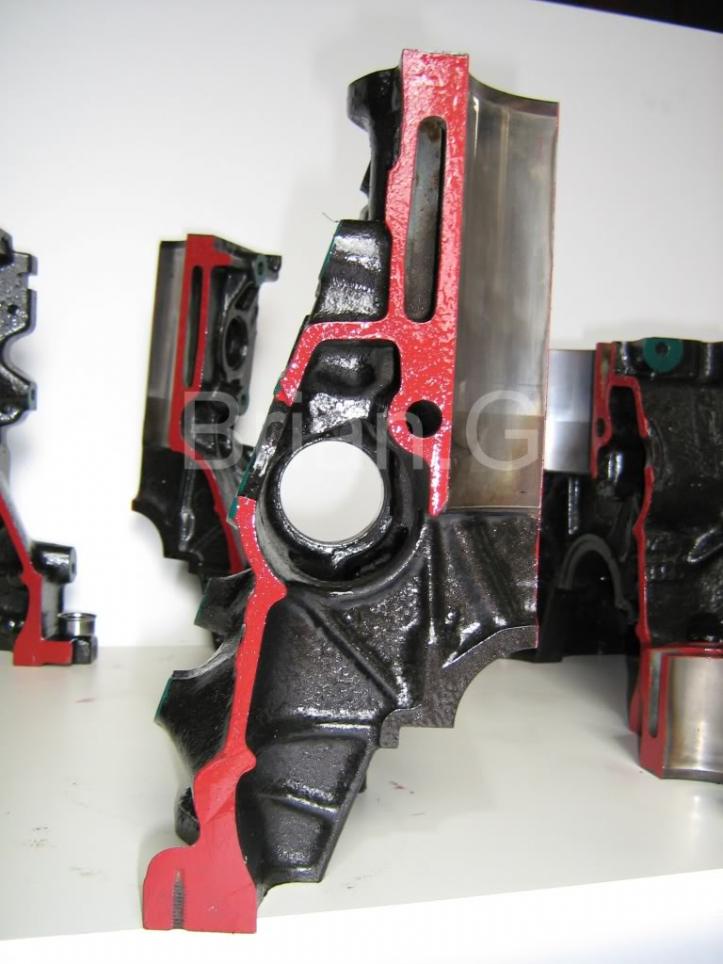
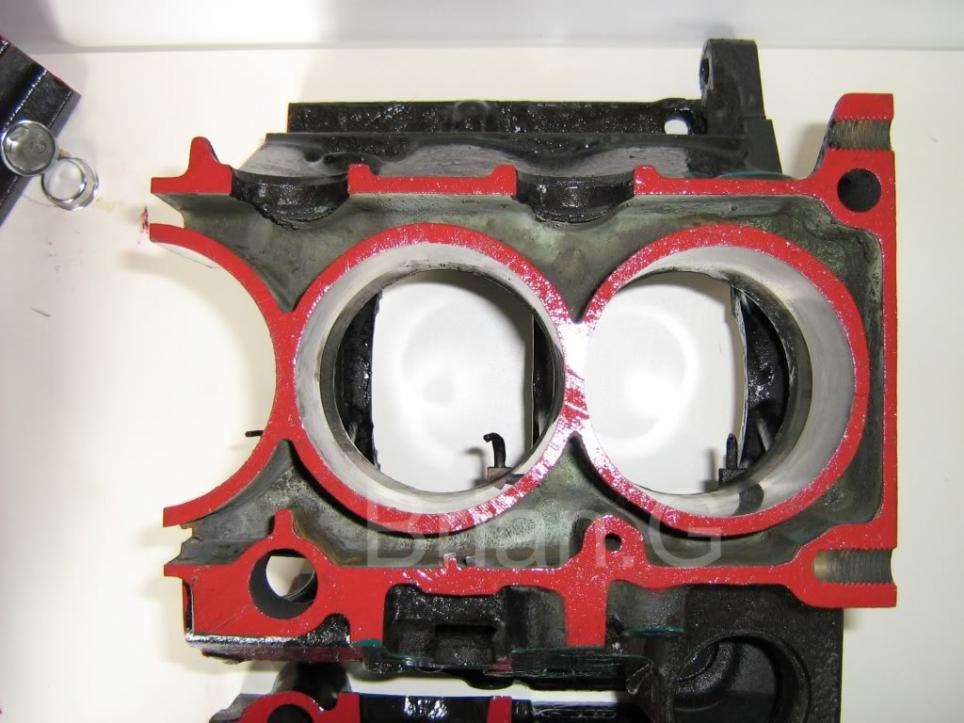
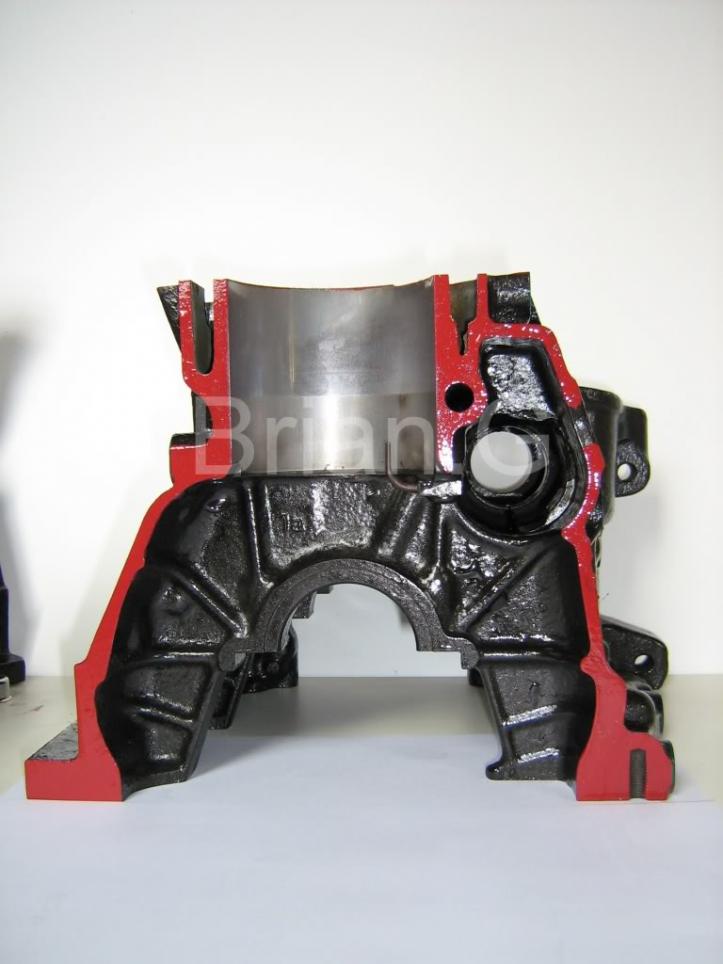
Should answer all questions in respect to how far out the 2.0l block can be taken to.
Here we go now, enjoy!
Engine code 6A.
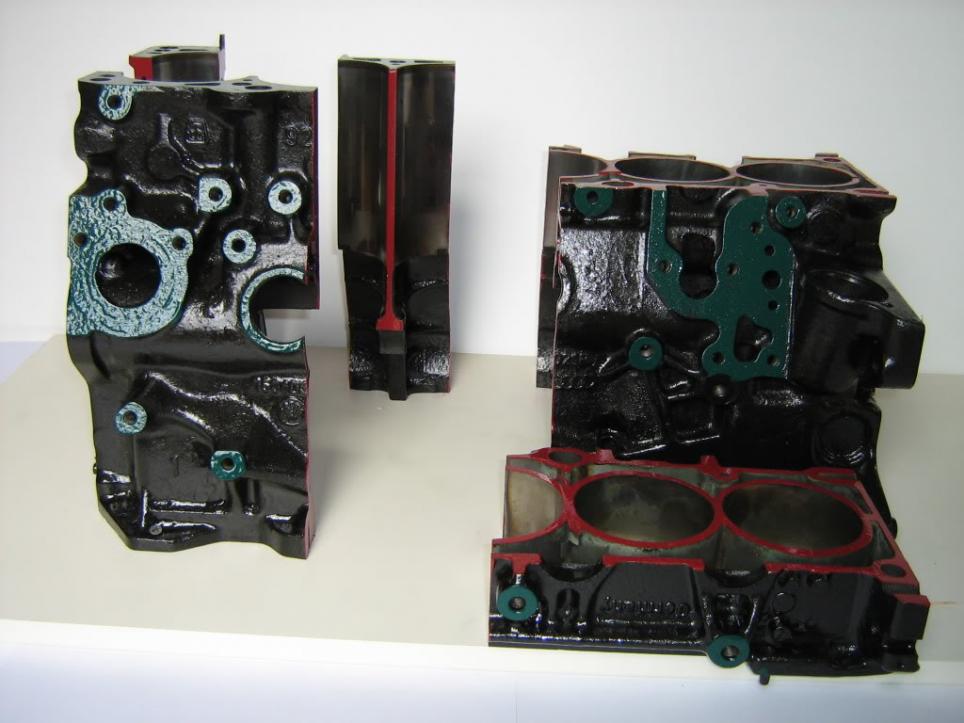
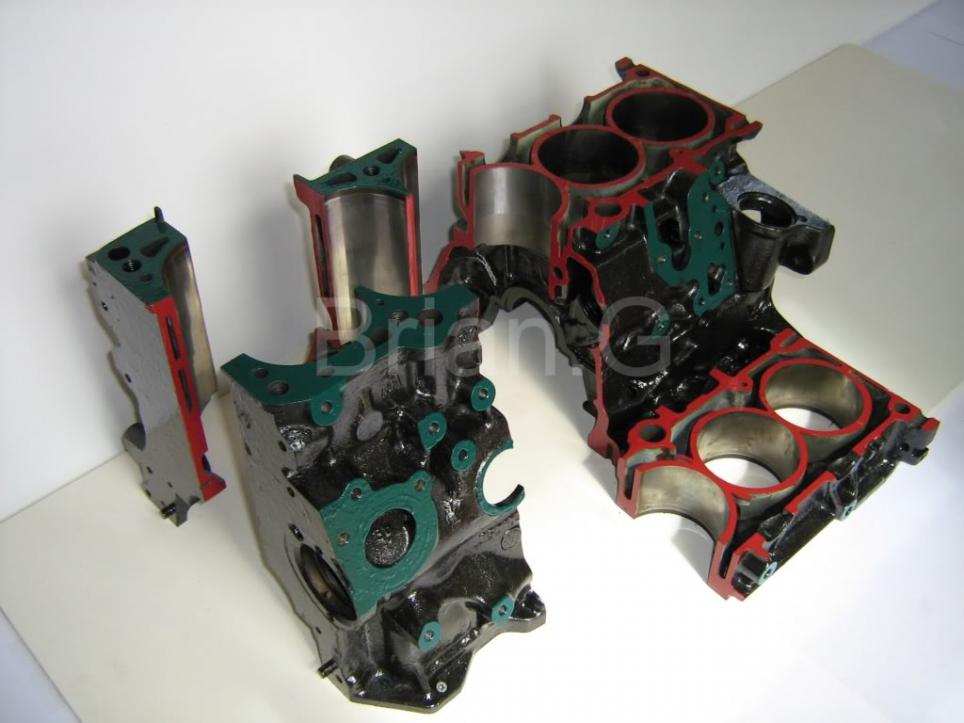
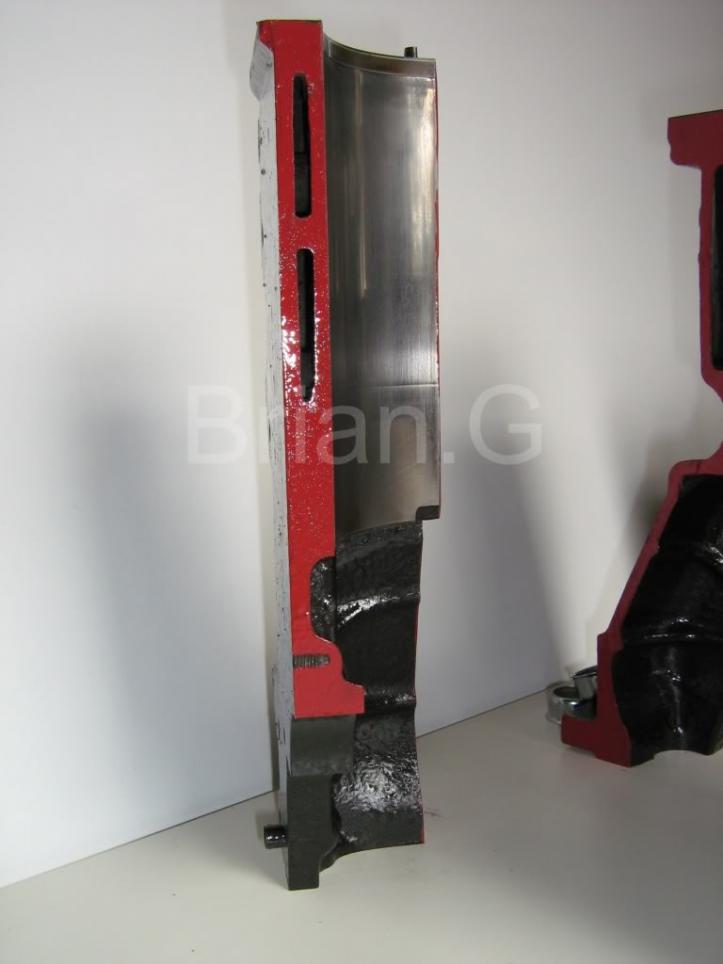
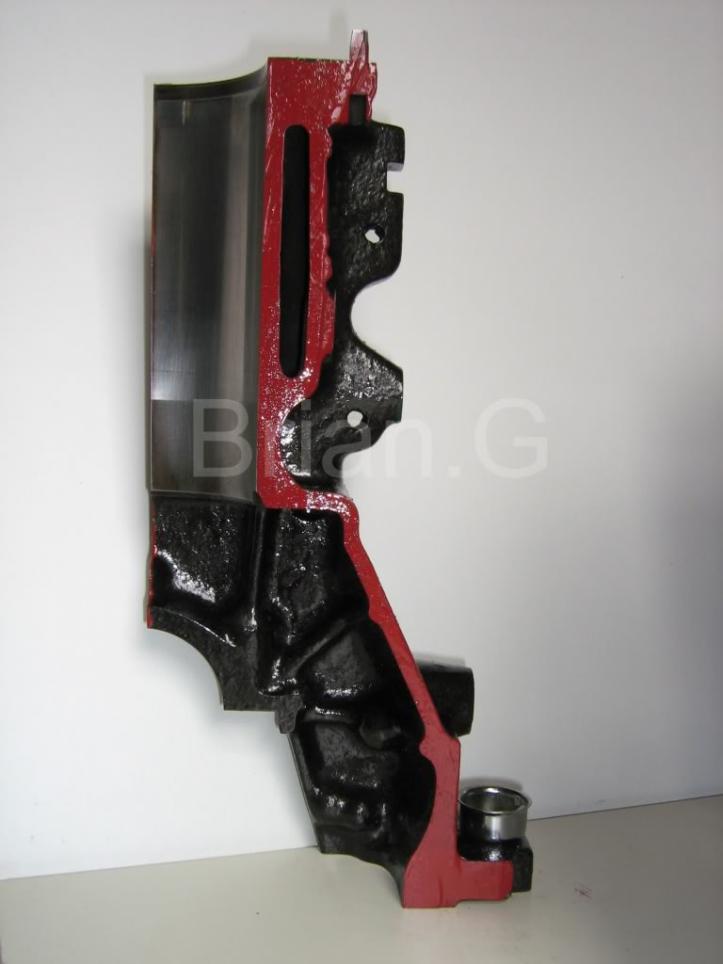
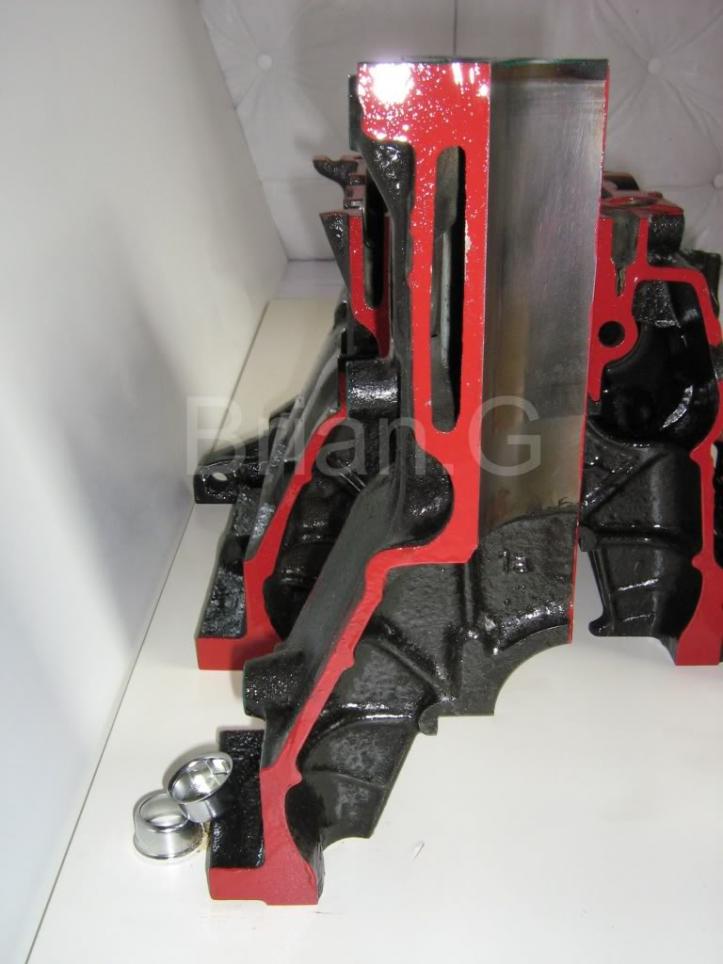
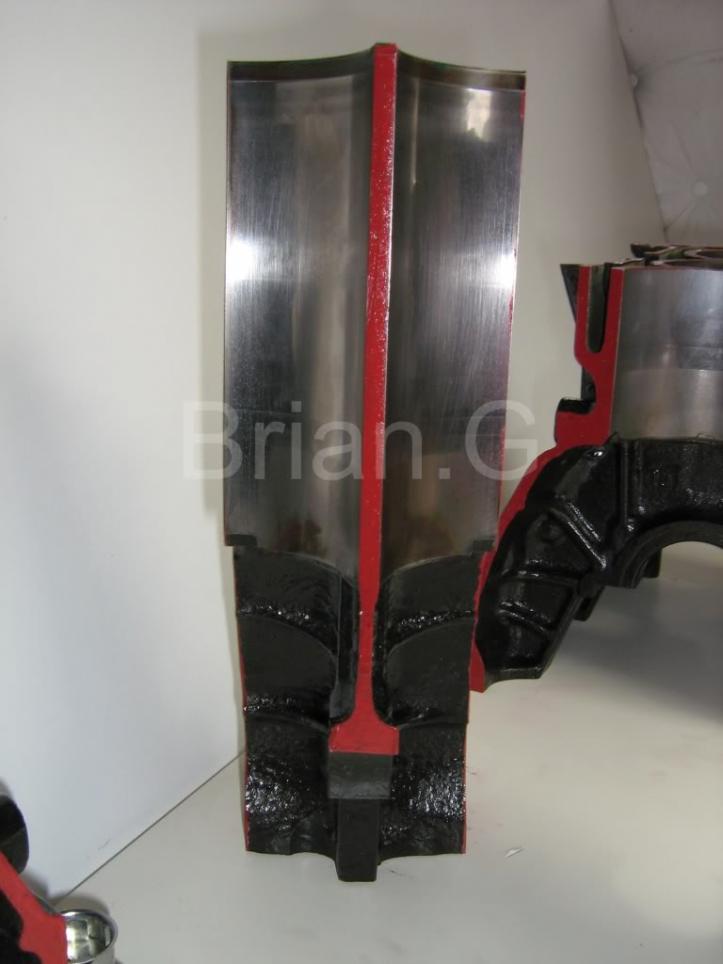
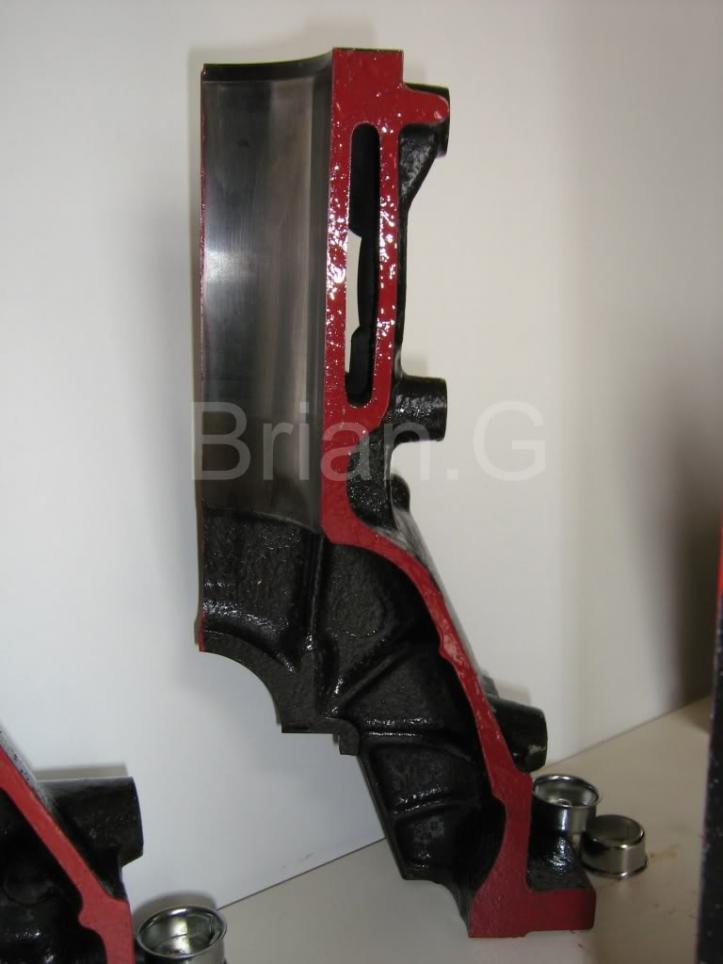
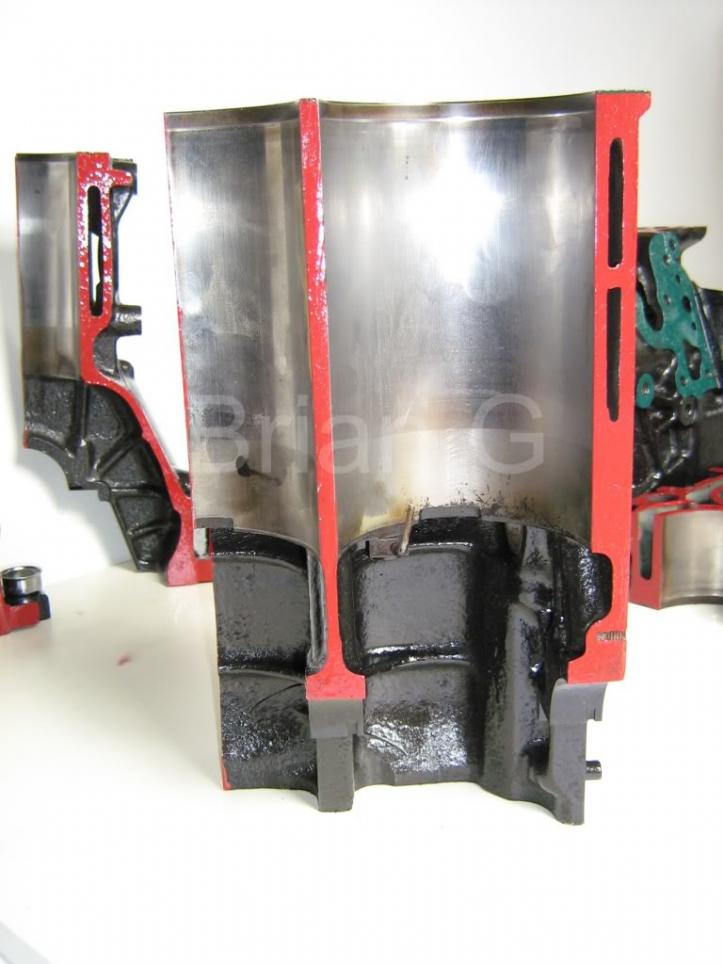
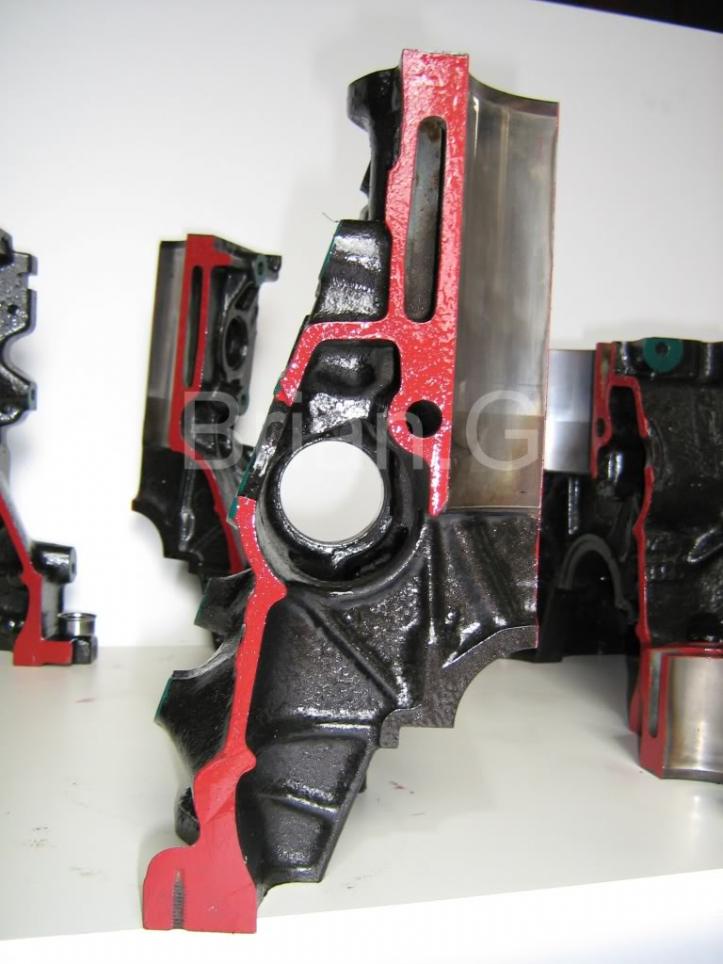
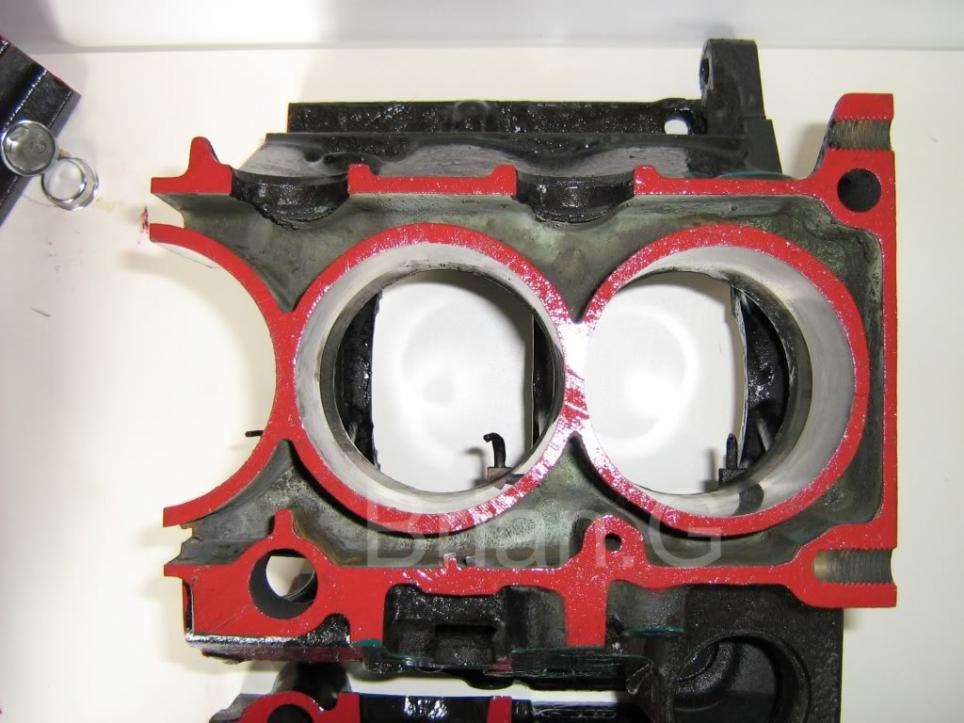
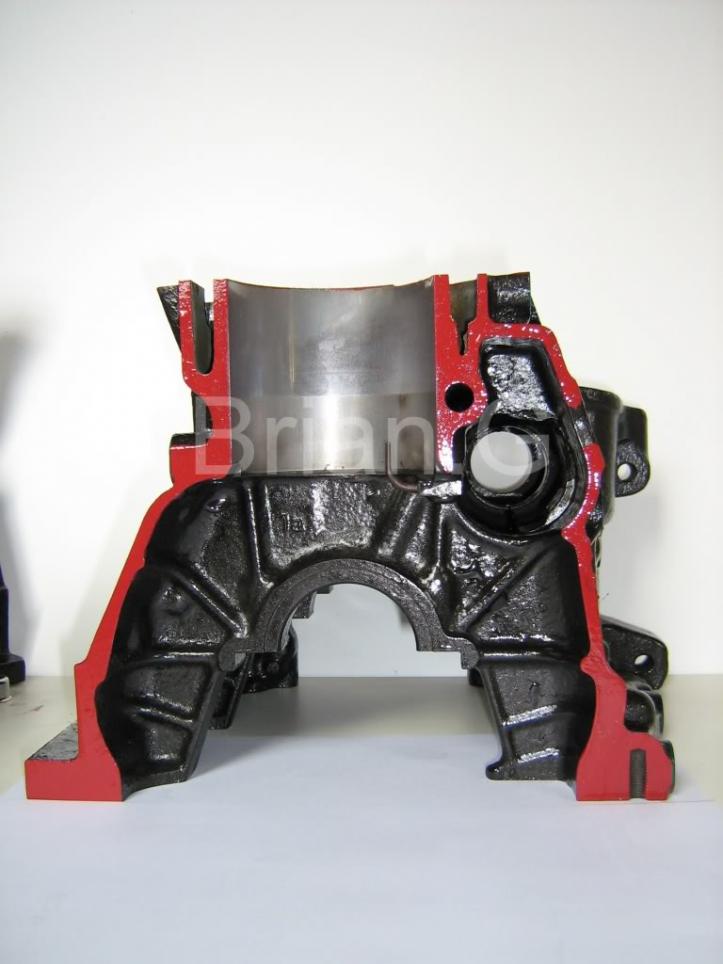
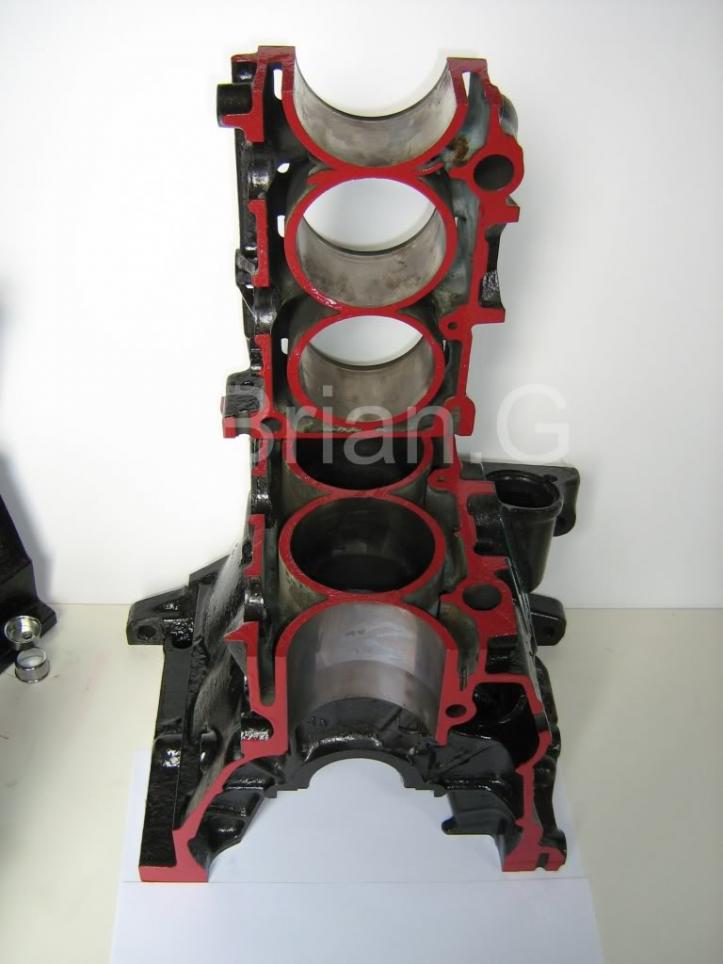
Comment